Laxmi Engineers
Welcome to our Website. Laxmi Engineers, a reputable manufacturer and supplier of a wide range of cement plants, packing machines, industrial crushers, feeder machines, and other items, was established in 1991. These machines were made by our trained professionals using top-notch raw materials and cutting-edge technology in Jodhpur, Rajasthan.
اقرأ المزيد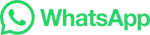