Rotary kiln process: An overview of physical mechanisms, …
The rotary kiln is used in many solid processes, including drying, incineration, heating, cooling, humidification, calcination and reduction. This widespread …
اقرأ المزيد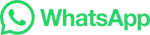
The rotary kiln is used in many solid processes, including drying, incineration, heating, cooling, humidification, calcination and reduction. This widespread …
اقرأ المزيدTHE SEMIDRY (LEPOL) KILN. The drying, the dissociation of the chemical water, the preheating to calcining temperature, and even partial calcination in this system takes place outside the rotary kiln, i.e, in the grate preheater.Hence, the rotary kiln proper has only to complete the calcination and form the clinker com· pounds. The length of the zones in …
اقرأ المزيدlater replaced by rotary kilns. Today, rotary kilns can be found as standard equipment worldwide. Today's annual global cement production has reached 2.8 billion tons and is and is expected to increase to about 4 billion tons per year. Major growth will be in countries located in Asia, as well as in regions such as the Middle East and North Africa.
اقرأ المزيدIn the rotary kiln, temperatures of the solid bed can be estimated and monitored by knowing the temperature of the kiln external wall and properties of the clay, kiln tube, and lining [90, 130]. The combustion of fuels and the calcination clay can be responsible for the emissions of pollutants, such as SOx, NOx, organics, etc. in the flue gas.
اقرأ المزيدRing formation is extremely common, occurring in roughly 85% of commercial rotary kilns. It is typically the result of a change in slagging temperature. …
اقرأ المزيدThe clinker exits the rotary kiln at ~ 1200 ... the calcium sulfate is added to control the initial hydration reactions of the cement and prevent rapid, or flash, setting. If coal is the sole fuel in use then a modem kiln will consume approximately 12 tonnes of coal for every 100 tonnes of clinker produced. Approximately 60% of the fuel input ...
اقرأ المزيد1. Introduction. The cement industry involves energy-intensive processes such as clinker rotary kilns and clinker grate coolers. Clinker is the fundamental component of the cement, which is produced through a baking process in a kiln and a subsequent cooling process in a cooler, and large amounts of thermal and electric energy are required [].In …
اقرأ المزيدCoating is a mass of clinker or dust particles that adheres to the wall of the kiln, having changed from a liquid or semiliquid to a solidified state. The solidified particles adhere to the surface of the coating (CS in Fig. 11.1), …
اقرأ المزيدControl and management of the technology by the above factors, the original service life of refractory to extend down to 14 to 16 months, kiln operation rate of over 85% to 90%, clinker production, mass They were all improved. Previous Post. factors affect the service life of the refractories are mechanical stress, thermal stress, production ...
اقرأ المزيدThe application on cement rotary kiln control is discussed in detail as a simulation example. In, a first principles model of a cement kiln is used to control and optimize the burning of clinker. An MPC strategy is used to stabilize a temperature profile along the rotary kiln, guaranteeing good combustion conditions and maximizing …
اقرأ المزيدPortland cement clinker is nodules (diameters, 5–25 mm) of sintered material produced by heating a homogeneous mixture of raw materials in a kiln to a sintering temperature of approximately 1450 °C for modern cements.The resulting clinker consists of four main minerals: 11 1. Alite or tricalcium silicate, Ca 3 SiO 5 (in oxide terms 3CaO.SiO 2), …
اقرأ المزيدThe nozzle is recommended to install below the axis of the furnace, to shift it to the side of the material by 0.05-0.1 diameter of the furnace and be sure to tilt downward at an angle …
اقرأ المزيدFirst, shut down the kiln, then check whether the inner lining is complete or not. After that, if the problem can't be solved, you should call the service after the sale immediately. The red kiln phenomenon can be seen in rotary kiln related production. After reading this post, you will capture the methods to prevent and solve the red kiln ...
اقرأ المزيدthe surface of the rotary kiln. Figure 1 illustrates the heat loss carried by the cement kiln working in the dry method. The greatest loss is the flue gas enthalpy equals of approx. 20% excess air enthalpy derived from the clinker coolers exceeding 12%, and heat loss from the surface of approx. 10%. Figure 1. Heat balance of cement kiln [4]
اقرأ المزيدRing formation is extremely common, occurring in roughly 85% of commercial rotary kilns. It is typically the result of a change in slagging temperature. The slagging temperature is the point at which the material will fuse together, allowing it to solidify. If a change in feed composition that reduces the slagging temperature is allowed to ...
اقرأ المزيدFigure 1:Section of Rotary Cement kiln on Pro-E graphics window.(Jan 2015) 1.1 Rotary kiln role in cement Production process. In cement production, rotary kilns are widely used to convert raw materials (raw meal) into cement clinker. Cement production is a combined physical and chemical process highly energy intensive which involves the
اقرأ المزيدA full-scale experiment was carried out in the rotary kiln burner of a cement plant by varying the SHW substitution rate from 0 to 3 t/hr. Clinker quality, emissions and other relevant operational ...
اقرأ المزيدManufacturing - the cement kiln. Most Portland cement is made in a rotary kiln. Basically, this is a long cylinder rotating about its axis once every minute or two. The axis is inclined at a slight angle, the end with the burner being lower. The rotation causes the raw meal to gradually pass along from where it enters at the cool end, to the ...
اقرأ المزيدAn example using this procedure is shown in Table 9.8 In the preceding pages tile chemistry of the kiln feed and clinker have been extensively discussed. The novice reader should now have a fairly broad knowledge of the many problems and factors that are associated with making cement clinker in a kiln.
اقرأ المزيدThe rotary kiln carries out several functions simultaneously. It is a device for conveying, mixing, heat transfer, and physical-chemical reactions. All these functions have to be in harmony. The ...
اقرأ المزيدMethods To Prevent Kiln Shell Deformation. Add the shell's rigidity. Use welding to replace the rivet because the rivet shell will cause the surface too smooth to lay refractory bricks and the rivet will lose when heating. So modern rotary kiln adopts welding shell with the advantages of simple structure, lower cost, lightweight, and good ...
اقرأ المزيدCement production in the rotary kiln began in 1895. Since then, the rotary kiln has been the main part of cement plants. It is in the rotary kiln that the basic chemical and physical reactions take place during the production of clinker. Rotary kilns are cylindrical steel tubes, slightly sloped from 2.5% to 4.5% and lined on the inside with ...
اقرأ المزيدRotary kilns are usually heated by direct contact of hot gas flowing in opposite direction with the bed (Fig. 1). The fuel is fed to a burner located at the end of the kiln, sometimes positioned in a separate chamber. ... (RoCKS): integrated modeling of pre-heater, calciner, kiln and clinker cooler. Chem. Eng. Sci., 62 (2007), pp. 2590-2607, 10 ...
اقرأ المزيدFigure 3.8.3. Rotary cooler. The modern rotary cooler is equipped with ceramic lining and lifters based upon the development of the planetary cooler. Special seals at the kiln outlet and the cooler inlet are required. To avoid …
اقرأ المزيدthe cement kiln system. Sulfur in cement kilns is derived from both kiln feed and from the kiln fuel. The form of the sulfur dictates the location in the kiln where the SO2 generation takes place. Sulfur in the fuel is oxidized in the burning zone or calciner, and is easily removed by reactive lime present in the kiln.
اقرأ المزيدClinker is cooled and ground with approximately 5 percent gypsum and other minor additives to produce Portland cement. The heart of clinker production is the rotary kiln where the pyroprocessing stage occurs. The rotary kiln is approximately 20 to 25 feet (ft) in diameter and from 150 ft to well over 300 ft
اقرأ المزيدteration algorithm for the rotary kiln balances (r = reactant, p = product, = advancement of reaction). Clinker bed temperature profile in the kiln and the cooler (with and without oxygen addition ...
اقرأ المزيدBlack-mix is made to nodules of size 6 — 8 mm before feeding to kiln with 12 to 13 % water or 0.13 x 1.63 = 0.212 kg water/kg clinker and this is the reason for manufacturing process is termed as semi-dry process. Kiln exhaust gas quantity remains as 2.29 kg with an average density 1.825 Nm³/kg. Material & Heat balance to produce 1 Kg ...
اقرأ المزيدThe Calcining Technology Of Clinker Kiln. Clinker kiln (cement kiln or cement rotary kiln) is the main equipment of cement plant. The clinker is formed by calcination in it. During the calcination process, raw meal powder is fed into the kiln cylinder from the top of the kiln tail. Due to the inclination and gentle rotation of the kiln cylinder ...
اقرأ المزيد1.1 Oxygen control. The oxygen at the calciner outlet is controlled through the calciner draft, in the same way as the oxygen at kiln inlet is controlled by the kiln …
اقرأ المزيد