Synthesis and characterization of cement clinker using …
The development of ordinary Portland cement (OPC) in the 18th century had a significant influence on urban societies, and it is still the most widely used material in the construction industry. In cement-clinker production, raw materials such as limestone, clay, sandstone, slag, and natural mixtures are commonly used (Schneider et al., 2011 ...
اقرأ المزيد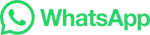