Overview of cement grinding: fundamentals, additives, technologies
Abstract. Grinding is an essential operation in cement production given that it permits to obtain fine powder which reacts quickly with water, sets in few hours and hardens over a period of weeks ...
اقرأ المزيد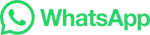