List of MP Birla Cement Plants in India
Initially a part of Reliance Cement Company Pvt. Ltd., the Butiburi plant was acquired by MP Cement in 2016. Its total installed cement production is 0.6 MTPA. Being a grinding unit, its main product is Portland Pozzolana cement (PPC). It employs the latest technology and machinery, making it one of the most modern plants in the country.
اقرأ المزيد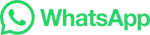