Review on vertical roller mill in cement industry & its …
Stacking & Reclaiming of Raw material: Swing type stacker & Reclaimer: Limestone & other raw material are stored in open area into a longitudinal storage unit called stockpile through Stacker. These are then extracted transversely from the stockpile through reclaimer: 3: Raw Meal Grinding & Homogenization: Grinding Mill - Vertical …
اقرأ المزيد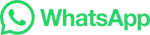