PROCESS TRAINING for operators of Vertical RAW …
For drying the wet raw material it is necessary that prior to the mill start up the grinding plant is.heated for some time.Otherwise the cold grinding …
اقرأ المزيد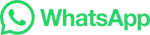
For drying the wet raw material it is necessary that prior to the mill start up the grinding plant is.heated for some time.Otherwise the cold grinding …
اقرأ المزيدThere are 210 large cement plants having total capacity of 410 MT cement production, with 350 small plants account for the rest. Out of 210 large units, ... The raw mill is either a Ball mill with two chambers or Vertical roller mill with inbuilt classifier. The hot gases from the pre heater enter the mill and are used for drying material in ...
اقرأ المزيدFinally, the strength tests (2–7 and 28-Days) and the chemical assays of the necessary samples were determined at cement plant by applying the standard procedures [18]. 2.2. ... Modeling and simulation of a fully air swept ball mill in a raw material grinding circuit. Powder Technol., 150 (2005), pp. 145-154.
اقرأ المزيدThe objective of this article is the development of a novel raw material mix proportion control algorithm for a cement plant raw mill, so as to maintain preset target mix proportion at the raw ...
اقرأ المزيدThe raw mill machine functions as a main material grinder in the initial milling process such as limestone, silica stone, clay, and iron sand to become raw mix. To find out the frequency of damage ...
اقرأ المزيدof a cement plant. Controlling the CF silo CF silo control is maintained either via a locally installed programmable control unit or by a central programmable control unit (see figure 7). The sequence of extraction from the seven outlets, the opening of the shut-off valves and the aeration of each segment is programmed in the control unit.
اقرأ المزيدRaw mill exhaust fans or stack fans are also called as de-dusting fans. In cement industry raw mill exhaust fans handle 2.2 ton of exhaust gases for the production of 1 ton of clinker. Raw mill exhaust fans are operated with very adverse situations because the fan handles mainly gases such as CO2, N2, NOx and Sox along with some dust particles.
اقرأ المزيدCoal Mill Function In Cement Plant Pdf. Nov 05, 2013 vertical raw mill cement industry pdf. design of raw mill in cement plant. OK raw mill Jul 10, 2017 The OK raw mill is the latest VRM offering from . It is designed with the same proven technology and modular design as the OK cement mill, which processes into just one unit, which simplifies ...
اقرأ المزيدThe energy efficiency equation of a raw mill system in the cement process is defined as: (44) η R M = m ˙ 2 h 2 + m ˙ 3 h 3 m ˙ 1 h 1 + m ˙ 4 h 4. 3.6. Exergy Efficiency. …
اقرأ المزيدThe objective of this study is to perform energy and exergy analysis of a raw mill (RM) and raw materials preparation unit in a cement plant in Turkey using the …
اقرأ المزيدA raw mill is a key piece of equipment used in a cement plant to grind raw materials into a fine powder. It works by crushing and grinding materials such as …
اقرأ المزيدRaw mill is mainly used for grinding cement raw meal in the cement factory production process. It is also suitable for metallurgical, chemical, electric power and other industrial mining enterprises to grind various ores and other grindable materials. Cement raw meal is a mixture of various raw materials before cement calcination.
اقرأ المزيدThe operation of the cement raw mill is a critical step in cement production. By grinding the raw materials into a fine powder, these powders can be more easily mixed with other cement ingredients and burn more evenly during the cement clinker process. Therefore, the efficient operation of the cement raw mill directly impacts the production …
اقرأ المزيدPart Three: Raw Mill. Process of Raw Mill The proportioned raw material is feed first to a grinding mill. In the mill, particles ground in to very fine sizes. In the grinding unit, drying, grinding and mixing takes place simultaneously. Hot gas from clinker burning unit is passed into the grinding unit to assist the drying and grinding process.
اقرأ المزيدA significant amount of false air can also enter through the inlet seal, in the case of the raw mill . installed to use kiln gases to dry the raw material. The largest false air intake takes place through the kiln inlet B and outlet A seals, due to the large . diameter of the seal and the continuous kiln rotary motion. 4.
اقرأ المزيدCement mill is another necessary cement equipment of the cement plant. After raw material crushing, cement mill plays vital role in the further cement manufacturing process. Cement ball mill, vertical cement mill, and cement roller press are common types of cement grinding plant. cement ball mill. Cement mill has two functions of the …
اقرأ المزيدFuels, burnability and characterization of cement raw meal. Vipin Kant Singh, in The Science and Technology of Cement and Other Hydraulic Binders, 2023. 6.4.6.1 Preblending of coal. Cement plants receive coal from more than one source, and even from the same source of supply, there are wide fluctuations in the ash content. Such fluctuations upset …
اقرأ المزيدPipes carrying compressed air and pneumatically conveyed pulverized materials like raw meal, coal and cement have to be able to withstand pressure of compressed air. Bends should have generous radius.
اقرأ المزيدFeeding Size: <25mm. get price! Air-swept coal mill is the main equipment of cement plant, also called coal mill in cement plant, used for grinding and drying various hardness of coal, crushing the coal briquette into pulverized coal. It is the important auxiliary equipment of pulverized coal furnace. The air-swept coal mill runs reliably ...
اقرأ المزيدControl instruments in a cement plant typically include PID controllers for the kiln and the mills, control valves for the raw mill and the cooler, and actuators for the feeders and the separators. ... Cement plant monitoring is essential for efficient production. It provides real-time data on the performance of the process, allowing for timely ...
اقرأ المزيدstudies were performed at vertical roller mill of ESCH Cement Plant, which is located in Luxemburg. ... raw data was made by reconciliation procedure presented for vertical roller mills (Aydogan ...
اقرأ المزيدAfter crushing, the raw materials are transported to the plant by conveyor. Before homogenized, the plant stores the material. Too finely ground, the materials are transferred to the raw mill, to produce raw mix. The raw mix is preheated before it goes into the kiln, and by the flame, it can be heated to 2000 °c to produce clinker.
اقرأ المزيد* Raw mill grinding area * Kiln area * Cement mill grinding area ... "Energy balance and cogeneration for a cement plant", Applied Thermal Engineering, 2002, 22, 485-494. [24] Tahsin E., Vedat A., "Energy auditing and recovery for dry type cement raotary kiln systems- A case study", Energy Conversion and Management 2005, 46, 551-562.
اقرأ المزيدSafety in Cement Plant M.E.-3C 2. Contents • Processes Involve • Hazards Involve in Operation • Safety Counter Measures 3. ... o Quarrying o Crushing o Clinker production o Milling processes at raw mill, cement milling and coal milling o Material transport o Storage o Use of hazardous material o Isolation• Special hazards as a result …
اقرأ المزيدA significant amount of false air can also enter through the inlet seal, in the case of the raw mill . installed to use kiln gases to dry the raw material. The largest false air intake takes …
اقرأ المزيدThe energy efficiency equation of a raw mill system in the cement process is defined as: (44) η R M = m ˙ 2 h 2 + m ˙ 3 h 3 m ˙ 1 h 1 + m ˙ 4 h 4. 3.6. Exergy Efficiency. The exergetic efficiency analysis provides some significant indicators about the process and its parts for efficient use.
اقرأ المزيدA cement mill is a fundamental component of the cement manufacturing process, playing a vital role in breaking down and grinding cement clinker into fine powder. This finely ground powder, when mixed with other materials, produces the building material we commonly know as cement. To achieve this crucial transformation, a cement mill …
اقرأ المزيدKeywords: cement; ball mill; conscious laboratory; random forest; support vector regression 1. Introduction In the cement industry, grinding is one of the most consuming energy stages in the production units. Around 65% of the total used electrical energy in a cement plant has to be utilized to grind raw materials, coal, and clinker [1,2].
اقرأ المزيدA raw mill is a key piece of equipment used in a cement plant to grind raw materials into a fine powder. It works by crushing and grinding materials such as limestone, clay, and iron ore into a ...
اقرأ المزيدContinuous blending involves simultaneous feeding of the silo, overflow to a second silo and final discharge to kiln feed. Modern equipment generally uses continuous CF silos, each having capacity of more than 24-hours' kiln feed and yielding a blending ratio (or 'blending factor') of 4-8, or around 2-3 for older silos.
اقرأ المزيد