Reducing energy consumption of a raw mill in cement industry
The raw mill considered in this study is located in a cement plant located in Sanliurfa, Turkey. The plant is a single chamber mill with mechanical circulation system …
اقرأ المزيد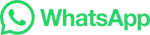
The raw mill considered in this study is located in a cement plant located in Sanliurfa, Turkey. The plant is a single chamber mill with mechanical circulation system …
اقرأ المزيدContinuous blending involves simultaneous feeding of the silo, overflow to a second silo and final discharge to kiln feed. Modern equipment generally uses continuous CF silos, each having capacity of more than 24-hours' kiln feed and yielding a blending ratio (or 'blending factor') of 4-8, or around 2-3 for older silos.
اقرأ المزيدA plant or a piece test. Whether you are looking for an entire cement plant or a single piece of equipment, we are the premium supplier. For new plants, we cover everything from evaluating initial quarry samples through to ongoing operation and maintenance services.
اقرأ المزيدUsing Eqs. (18)– (21) and the data on the and total heat output is obtained. RM given above along with Tsf = 343 K, Tin = 401.66 K and Tout = 295 K, the grinding room total heat losses in 4.4. Energy and exergy efficiencies of the raw mill Section 1 were calculated to be 1 356 146.68 W. (b) Section 2.
اقرأ المزيدSafety Labeling. • Attach labels and safety pre-cautions to serve as a guide to the workers. • Attach directions and labels for emergency exits. • Place the label to where they are easily seen lest they become useless. • All workers should have their own materials according safety operations and others.
اقرأ المزيدKeywords: Vertical roller mill, cement grinding, performance evaluation INTRODUCTION Cement production is highly energy consuming process with energy utilization of around 110-150 kWh/t (Villa, 2005).
اقرأ المزيدRaw mill is mainly used for grinding cement raw meal in the cement factory production process. It is also suitable for metallurgical, chemical, electric power and other industrial mining enterprises to grind various …
اقرأ المزيدRaw mill exhaust fans or stack fans are also called as de-dusting fans. In cement industry raw mill exhaust fans handle 2.2 ton of exhaust gases for the production of 1 ton of clinker. Raw mill exhaust fans are operated …
اقرأ المزيدThe raw mill system is an important component among other parts of the cement plant. Because the raw mill system is used to grain the crude inputs into the …
اقرأ المزيدThe objective of this article is the development of a novel raw material mix proportion control algorithm for a cement plant raw mill, so as to maintain preset target mix proportion at the raw ...
اقرأ المزيدThe exergy destruction rate and exergetic performance of the raw mill system in the cement plant were calculated to be 2940 kW and 34.67%, respectively. In …
اقرأ المزيدA raw mill is a key piece of equipment used in a cement plant to grind raw materials into a fine powder. It works by crushing and grinding materials such as limestone, clay, and iron ore into a ...
اقرأ المزيدAPPLICATION CRITICALITY. The rotary kiln is the heart of a cement manufacturing plant. Cement kilns have all chemical ingredients. These. ingredients are at a broad range of gas temperatures from 100° to 1650°C. The emissions contain: High concentrations of alkaline solids, including sodium and potassium oxides; High concentrations of freshly ...
اقرأ المزيدAs a trusted cement plant manufacturer of China, AGICO Cement can provide high-quality cement mill and other kinds of cement equipment at competitive prices. Wide product range: For meeting various requirements from different clients, our cement mill range from cement ball mill, vertical cement mill, Raymond mill, coal mill in cement plant, etc.
اقرأ المزيدThe cement rotary kiln. When operating the vertical roller mill, the operator must control the inlet and outlet air valves to make the air volume of the system in a balanced state, so as not to affect the air pressure at the back end of the rotary kiln. We are AGICO, a professional cement equipment manufacturer and cement plant contractor.
اقرأ المزيدFigure 2.3.18. Ball mill in operation at a cement plant. ... The operational data of the mill system are given in Table 2.3.8. Table 2.3.8. Typical Operational Data of a Plant …
اقرأ المزيدWater injection is one way to control and maintain the cement temperature at mill outlet at a preset level. Depending on the circuit thermal balance analysis and the mill design, Magotteaux water injection system automatically sprays water into the mills in 3 different ways: 1st chamber via its inlet. 2nd chamber via mill outlet or via mill ...
اقرأ المزيدProcess of analysis of the occasional breakdowns in raw mill process. 2.1. Data Collection The collection of the data was performed from 1 31 August 2023 in the Raw Mill Department of PT X for the CC-2 raw mill mach ine. The collected data used for evaluation of OEE consist of operation time each day, breakdown time each week, and …
اقرأ المزيدPower Distribution in Cement Plant. ... so vertical roller mills can also grind the white cement raw material [15], [16]. • Installation of vertical roller mill system requires less space than a closed system Ball mill circuit. Capital investment is just 70% of the closed ball mill system ...
اقرأ المزيدIn order to produce raw materials preparation, clinker and rotary kilns are widely used in cement plants. The objective of this study is to perform energy and exergy analysis of a raw mill (RM) and raw materials preparation unit in a cement plant in Turkey using the actual operational data. The RM has a capacity of 82.9 ton-material hourly.
اقرأ المزيدA raw mill is a key piece of equipment used in a cement plant to grind raw materials into a fine powder. It works by crushing and grinding materials such as …
اقرأ المزيدCement Vertical Mill Grinding System. Cement vertical mill, also called roller mill, is another raw mill commonly used in cement plants. Compared with the cement ball mill, …
اقرأ المزيدThe Cement Plant Operations Handbook is a concise, ... Raw materials management system – 22. Concrete problems 16 1. Raw materials – 2. Raw mix – 3. Reserves – 4. …
اقرأ المزيدProcessed material: Clinker. Capacity: 50TPD. Feed size: 30mm. Discharge size: 100 mesh. Fote raw mill working site in Kenya. This raw mill is used in the material preparation of cement. The capacity is large enough to meet the requirement and the product has uniform fineness, which helped Fote get good feedback from our customer.
اقرأ المزيدOur best-in-class OK™ Mill is a globally successful vertical roller mill solution for grinding raw material, cement and slag. Its cutting-edge design features consistently deliver the highest quality products with the greatest efficiency. It is affordable to install and cost effective to operate over your cement plant's lifetime.
اقرأ المزيدAfter crushing, the raw materials are transported to the plant by conveyor. Before homogenized, the plant stores the material. Too finely ground, the materials are transferred to the raw mill, to produce raw mix. The raw mix is preheated before it goes into the kiln, and by the flame, it can be heated to 2000 °c to produce clinker.
اقرأ المزيدSemantic Scholar extracted view of "Reducing energy consumption of a raw mill in cement industry" by A. Atmaca et al. ... Chapter 2.25 – Thermodynamic Performance Analysis of a Raw Mill System in a Cement Plant. Mehmet Altinkaynak M. Ozturk A. Yakut. Engineering, Environmental Science. 2018;
اقرأ المزيدOur range of specialised sampling devices service all the routine sampling programs across the cement plant. They are designed to operate at frequent intervals (every ½, 1, 2, 4, 8 hours or longer) during normal operation. These samplers are permanently installed at designated locations and usually operate fully or semi-automatically.
اقرأ المزيدYamama Cement ordered two 10,000 tons per day kiln lines. For raw material grinding four QMR² 48/24 are contracted, while for cement grinding four polycom® high pressure grinding rolls as a combi grinding system are considered due to material properties. The four mills are operating very successful since mid of 2021.
اقرأ المزيدAs a leading cement grinding plant manufacturer in China, we offer roller press in cement plant, roller press cement mill, high pressure grinding roller, Get your free quote now!. ... raw material of cement, ... roller press helps ball mill system to increase the output by 30-50%. The 0.08mm fine material in the extruded material cake accounts ...
اقرأ المزيد