Design of horizontal ball mills for improving the rate of
The ball mill used in this study was a PM400 planetary mill manufactured by Retsch, Germany. ... View PDF View article View in Scopus Google Scholar [2] A.K. Hall, J.M. Harrowfield, R.J. Hart, ... The use of the discrete element method and fracture mechanics to improve grinding rate prediction. Miner. Eng., 14 (2001), pp. 565-573.
اقرأ المزيد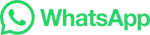