(PDF) Coarse Return Prediction in a Cement Industry's Closed Grinding …
The cement grinding process is a complex industrial process which is composed of multiple sub-processes and the variables are coupled each other, according to the characteristic, a multi-variable ...
اقرأ المزيد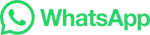