Experimental investigation of the impact breakage …
The novelty of this study is that a drop-ball experimental setup was designed, which can simulate the impact contact behavior between steel ball and particle in a ball mill. The effect of particle size, impact energy, and impact number on the iron ore particle impact breakage characteristics were analyzed to reveal the particle breakage ...
اقرأ المزيد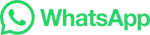