Improved iron-ore sinter for blast furnaces | Steel in Translation
Technology has been developed for the production of fluxed local sinter and pellets with residual carbon for blast-furnace use. The new products have better metallurgical characteristics than existing materials. ... Gogenko, O.A., et al., Production of an experimental batch of iron-ore pellets with residual carbon at Seversk enrichment …
اقرأ المزيد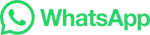