Energy integration of sponge iron production process
Sponge iron is produced primarily both by using non-coking coal and natural gas as reductant and therefore classified as coal based and gas based process respectively. …
اقرأ المزيد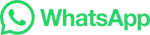
Sponge iron is produced primarily both by using non-coking coal and natural gas as reductant and therefore classified as coal based and gas based process respectively. …
اقرأ المزيدAbout Sponge Iron. Direct-reduced iron (DRI), also called sponge iron, is produced from the direct reduction of iron ore (in the form of lumps, pellets, or fines) by a reducing gas produced from natural gas or coal. The reducing gas is a mixture, the majority of which is hydrogen (H2) and carbon monoxide (CO), which act as reducing agents.
اقرأ المزيدSteel making contributes 6% of global CO2 emission (including associated power emissions). Blast furnaces dominate global production, have long capital lives, and resist adoption of decarbonization technology. Deep decarbonization and net-zero production will require both asset replacement from BF to DRI+EAF and development …
اقرأ المزيد5. THE PRESENT SCENARIO OF THE INDUSTRY India has one of the richest reserves of all the raw materials required for the industry, namely land, capital, cheap labour, iron ore, power, coal etc. Yet we are 4th in the world ranking for production of steel. We produced 66.8 million tonnes in 2010-11, while China, at the top of the list, …
اقرأ المزيدIndia is the world's largest producer of sponge iron, accounting for 13 per cent of the global production 8. Sponge iron is produced using either coal or natural gas. Since coal is available in India, the sector largely depends on coal based sponge iron which contributes about 80 per cent of the total capacity in the country9.
اقرأ المزيدPage 12. ROTARY COOLER. The product is conveyed to the product separation and storage building. The product is Sponge iron and char. Place that spraying a controlled amount of water directly into hot solids and by spraying additional water outside the cooler shell. Page 13. SCREENING. + 10 mm 3-10 mm - 3 mm.
اقرأ المزيدcrude steel producer in the world and the largest producer of sponge iron. As per official estimates, the Iron and Steel Industry contributes around 2 per cent of the Gross Domestic Product (GDP) and employs about 25 lakh people directly or indirectly. From a negligible global presence, the Indian steel
اقرأ المزيدAbstract. Titanium sponge is widely produced employing the Kroll process of high-temperature reduction of titanium tetrachloride by magnesium. The technological developments over the last few decades have focused on cost/energy savings in addition to introducing sophisticated systems in the manufacturing technology.
اقرأ المزيدManufacturers Association. The Sponge Iron Manufacturers Association (SIMA) established in 1992 is an all India apex body of Indian sponge iron industry. It is the voice of the indian iron ore based sponge iron & steel industry, at both domestic and global forums. As a not-for-profit society, SIMA has been mandated to communicate the …
اقرأ المزيدThe production volume of gas-based sponge iron in India accounted for around 8.12 million metric tons at the end of 2022. It reflected a decrease from the previous year's 8.4 million metric tons ...
اقرأ المزيدproduction for sponge iron and, to some extent, cast iron depend on the growth of arc steelmaking. Arched steelmaking capacity outside China has grown at a rate of 5 to 6 percent over the past 30 to 40 years. The World Iron and Steel Association believe that this growth is likely to continue, and we will see a commensurate growth in demand for ...
اقرأ المزيدThe direct reduced iron market size is anticipated to reach USD 131.32 Billion by the end of 2036, expanding around 9.26% CAGR during the forecast period i.e., 2024-2036. Asia Pacific industry is predicted to cross USD 66.27 billion by 2036, impelled by a major hub for steel production, with countries such as China, India, and Japan …
اقرأ المزيدEstablished on September 28, 2004, RSIPL has consistently led the industry with innovation and sustainability as the cornerstone of our mission. As part of the esteemed M.P. Rungta Group, RSIPL stands as a symbol of excellence in sponge iron production. Leveraging cutting-edge technology, we redefine the boundaries of possibility in our field.
اقرأ المزيدIndia Sponge Iron: Production data was reported at 4,496.000 Metric Ton th in Jan 2024. This records a decrease from the previous number of 4,526.000 Metric Ton th for Dec 2023. India Sponge Iron: Production data is updated monthly, averaging 2,835.000 Metric Ton th from May 2013 to Jan 2024, with 129 observations. The data reached an all-time high …
اقرأ المزيدShangliao Sun. Around 80.7 percent of the sponge iron produced in India in 2022 was under coal based process route. This was due to numerous coal based units present in the mineral rich states ...
اقرأ المزيدblast air to form molten reduced iron, carbon monoxide (CO), and slag. The molten iron and slag collect in the hearth at the base of the furnace. The byproduct gas is collected through offtakes located at the top of the furnace and is recovered for use as fuel. The production of 1 ton of iron requires 1.4 tons of ore or other iron bearing ...
اقرأ المزيد• India was the largest producer of Sponge Iron in the world in 2021. The coal-based route accounted for 77% of total Sponge Iron production (39.03 mt) in the country in 2021-22 (provisional). • Data on production of Pig Iron, Sponge Iron and Total Finished Steel (alloy/stainless + non-alloy) are given below for last five years:
اقرأ المزيد5. The substitution of scrap by sponge iron has some limitations depending on the furnace operating conditions. Only 20% to 30% of sponge iron can be used in the furnace …
اقرأ المزيدThis product is known as direct reduced iron (DRI) or sponge iron. Processes that produce iron by reduction of iron ore (in solid state) below the melting point are generally classified as DR ...
اقرأ المزيدDRI Processes – Types using Steam Reforming HYL type flowsheets Midrex type flowsheets Lookalikes exist in each category. Read more. Technology Business. 1 of 7. Download Now. Download to read …
اقرأ المزيدxyk process for sponge iron production ppt – Crusher South Africa tunnel kiln process sponge iron | Solution for Mining… HOT STONE CRUSHING PLANT » 40TPH - 60TPH Crusher Plant
اقرأ المزيد1 of 16. Download Now. Download to read offline. Production of Direct Reduced Iron in Rotary Hearth Furnace - Download as a PDF or view online for free.
اقرأ المزيدIn this paper, the production process of sponge iron in rotary kilns from the perspective of mechanics and chemistry is investigated. Keywords: Sponge iron, rotary kilns, alloying, …
اقرأ المزيدThe reduction of iron oxides takes place according to the following chemical equations: Fe2O3 Fe2O3 + 3CO + 3H2 → 2Fe → 2Fe + 3CO2 + 3H2O (1) (2) (1) F e 2 O 3 + 3 C O → 2 F e + 3 C O 2 (2) F e 2 O 3 + 3 H 2 → 2 F e + 3 H 2 O. In contrast to the blast furnace process, the direct-reduced iron process operates at temperatures of up to ...
اقرأ المزيدSponge Iron Industry - Download as a PDF or view online for free ... Ppt_on_steel_making.ppt. Ppt_on_steel_making.ppt kayow1 ... DRI is preferred in India because of 1.Small scale of production. …
اقرأ المزيدIndia is the largest producer of direct reduction of iron (DRI), popularly known as sponge iron and accounted for about 39.3% of the global production in 2020. India's growing …
اقرأ المزيد3. CONSULTING ENGINEERS LIMITED INTRODUCTION TATA CONSULTING ENGINEERS LIMITED In Direct Reduction route, Ore is reduced at a temperature of 900-1050 oC, in the solid state (below the melting point) by : Carbon Monoxide (Coal Based). Or Hydrogen & Carbon Monoxide (Gas Based) The reducing …
اقرأ المزيدFour sponge iron (SI1, SI2, SI3, and SI4) plants with different installed capacity and sponge iron (SI) production have been considered for studies based on the baseline …
اقرأ المزيدThe coal based direct reduction rotary kiln process was developed for converting iron ore directly into metallic iron without the melting of the materials. The process has the advantage of low capital expenditure and no requirement of coking coal. The metallic iron in this process is produced by the reduction of iron oxide below the …
اقرأ المزيد