Extraction of antimony from a hydrochloric acid side stream …
Potential candidate secondary sources of antimony include the by-products of pyrometallurgical copper extraction and refining. The final stage of the copper process involves electrolytic refining from 99.7%-pure copper anodes. These anodes contain impurities from ore concentrates, which are incorporated in the electrolyte along with …
اقرأ المزيد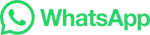