Modeling and Optimisation of Spiral Concentrator for
Experiments were carried out using a spiral concentrator test rig containing feed conditioner, centrifugal pump and a spiral concentrator with feed to spiral and recirculation. Time samples of concentrate and tails were collected, weighed, dried analysed. Regression equations were developed for Concentrate yield, grade and …
اقرأ المزيد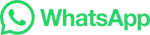