Tin ore processing | Commodities | Mineral Technologies
Recovery of tin bearing minerals from hard rock deposits involves multiple processing stages. Mineral Technologies can aid the processing of historical tin tailings by designing a suitable gravity circuit comprising spirals and wet shaking tables that will recover tin minerals down to approx. 38 microns.. Pictured below is a pilot plant, designed and built …
اقرأ المزيد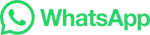