The cement kiln
A development of this process is the 'precalciner' kiln. Most new cement plant is of this type. The principle is similar to that of the dry process preheater system but with the major addition of another burner, or precalciner. With the additional heat, about 85%-95% of the meal is …
اقرأ المزيد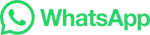