Energy efficiency of cement finish grinding in a dry batch …
In the cement industry, the clinker grinding step consumes about one-third of the power required to produce one ton of cement. This refers to an average specific power consumption of 57 kWh per ton [1]. Such large amounts of energy justify the need to improve the energy efficiency of comminution process.
اقرأ المزيد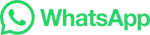