Chapter 17: Grinding Methods and Machines
Updated Parting and Grooving Concept. Oct. 5, 2023. Cutting Tools. Cutting Tool Applications, Chapter 17: Grinding Methods and Machines. June 29, 2020. …
اقرأ المزيد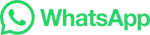
Updated Parting and Grooving Concept. Oct. 5, 2023. Cutting Tools. Cutting Tool Applications, Chapter 17: Grinding Methods and Machines. June 29, 2020. …
اقرأ المزيدSafe Operation of Grinding Machines 1- Read the Manual. Before using a grinding machine, it is important to read the manual carefully. The manual will provide information on the proper use of the machine, including safety instructions, operating procedures, and maintenance requirements. ... Here are the steps to perform a ring test: …
اقرأ المزيدSurface grinding is an abrasive machining process, creating flat, smooth finishes on workpieces using a spinning wheel with rough particles, essential for precision manufacturing. This blog post will delve deep into surface grinding, highlighting its importance, techniques, and applications in modern manufacturing. Keep reading.
اقرأ المزيدWhat are the Parts and Functions of the Grinding Machine? Base: The base is a cast iron-made body that houses all the components of the grinding machine. Table: This part holds the material to be grounded and allows it to rotate around a vertical axis. It supports and holds the workpiece firmly in place for accurate grinding operation.
اقرأ المزيدSpeed lathes are commonly used for tasks like polishing, grinding, and sanding, as well as for small-scale production of simple cylindrical shapes. ... Turning: Turning is the primary operation performed on a lathe machine. It involves removing material from the workpiece to create a cylindrical shape. The cutting tool is fed parallel to the ...
اقرأ المزيدGrinding machines offer several advantages, including: They can achieve high levels of precision and accuracy. These versatile tools can perform a wide range of …
اقرأ المزيد9. Grinding. Grinding operation may be performed in a drilling machine to finish a hardened hole. The grinding wheel is made to revolve with the spindle and is fed up and down. A suitable grinding wheel may be selected for surface grinding operation. Grinding can also be done correctly out of roundness of the hole.
اقرأ المزيد· Grinding operation may be performed in a drilling machine to finish a hardened hole. · Grinding wheel is made to revolve with the spindle and is fed up and down. · Accuracy in grinding operation is ± 0.0025 mm.
اقرأ المزيد4. Tapping: In tapping, a tap is used for making internal threads. That means tap works as a cutting tool inside the tapping. Tapping in a drilling machine can be performed by hand. Or you can also use any external power for doing this. The metal is removed, when the tap is inserted into the hole.
اقرأ المزيدTurning is a machining process performed on a machine in which the cutting tool (non-rotary tool bit) follows a helix tool path by moving linearly along the workpiece.. Turning traditionally refers to the action of cutting external surfaces, whereas "boring" refers to the action of cutting internal surfaces (holes). Thus, the phrase "turning and boring" …
اقرأ المزيدDrilling Machine Definition: A drilling machine is a type of machine in which the holes are being made on the workpiece by making use of a rotating tool called drill bit or the twist drill. Drilling is basically a technology of creating holes. Drilling operations can also be performed on Lathe machines.
اقرأ المزيدThe drilling machine is the second most important machine tool in a workshop. 9. The drilling machine was primarily designed to originate a _____. 10. For drilling operation, the drill rotates with_____ pressure if job is held on earth. Sanfoundry Global Education & Learning Series – Machine Tools and Machining.
اقرأ المزيدEvan Doran. Associate Editor, Modern Machine Shop. On its surface, grinding seems simple: a machine takes a rotating tool (usually a wheel) with abrasive grains and applies it to a workpiece's surface to remove material. Each grain is its own miniature cutting tool, and as grains dull, they tear from the tool and make new, sharp grains prominent.
اقرأ المزيدInitial Investment: Grinding machines, especially those used for precision applications, are costly. High-end machines with advanced features like CNC systems are even more expensive. Basic Grinding Machines: Entry-level grinding machines, suitable for small-scale operations or less complex tasks, typically range from $5,000 to $20,000.
اقرأ المزيدIn these articles we will try to learn Definition, Parts, Operation we perform on it, The Types, Specification advantages, disadvantages, and application of lathe machine. Lathe Machine Introduction: Lathe machine is probably the oldest machine tool know to mankind. Its first use dates back to 1300 BC in Egypt. ... Grinding Machine: …
اقرأ المزيدIt is a method of producing a flat surface at right angles to the axis of the cutter. This operation produces a flat surface at the face on the workpiece. This surface is perpendicular to the surface prepared in plain milling …
اقرأ المزيد520-548-7328. kip@kahmco. Kip Hanson is a contributing editor for Cutting Tool Engineering magazine. Contact him by phone at (520) 548-7328 or via e-mail at kip@kahmco. Ralf Schürl, who co-authored this report, is area sales manager for Schaudt/Mikrosa, of United Grinding, and technical sales support for United Grinding …
اقرأ المزيدThe crankshaft grinding wheel is secured with a hub, balanced and mounted to the machines arbor to accommodate operation at high RPMs. The surface finish on most grinding wheels is 54 grit, which is a similar specification as used for sandpaper. The most common grinding wheels accommodate an arbor size of 3", 5" and 8" for industrial ...
اقرأ المزيدThis article explores 19 types of grinding machines and examines how they work, how they differ, and how much they might cost you. 1. Angle Grinder. An angle grinder, also referred to as a side grinder, uses a grinding disc to cut, deburr, polish, and clean. Angle grinders are unique in that they're portable, handheld devices.
اقرأ المزيدGrinding Machine Definition. A grinding machine or grinder is an industrial power tool that uses an abrasive wheel for cutting or removing the material.It is a process of metal cutting by using a rotating abrasive wheel from the surface of the workpiece. Generally, the grinding is a type of finishing operation to make sure that there is high …
اقرأ المزيدYou can swivel the work-head for doing taper grinding operation. Your machine has a coolant system to flood the cutting area during grinding. ... The possibilities are infinite in your CNC Grinders and machines can be built depending on the grinding operations to be performed. Your CNC grinder may have provision for wheel balancing.
اقرأ المزيدMilling Machine Definition: The milling machine is a type of machine which removes the material from the workpiece by feeding the work past a rotating multipoint cutter.The metal removal rate is higher …
اقرأ المزيدCenterless grinding is a precise and efficient machining process used to remove material from a workpiece without the use of a grinding machine. This process is ideal for cylindrical and bar grinding, resulting in an excellent surface finish and tight tolerance.In this ultimate guide, we will cover everything you need to know about centerless grinding, including its …
اقرأ المزيدThe specific grinding operation being performed; High-precision grinding machines can achieve even better accuracies, often in the range of 0.0001 inches …
اقرأ المزيدThe buffing wheel is attached to the bench grinder to perform the buffing operations which preserve the real texture of the material. A tank or bucket of water is used as a coolant …
اقرأ المزيدThe usage of a machine can be extended still further to include screw cutting, turning, planetary grinding, or gear cutting. The cutting tool is normally single point which are made of M2 and M3 high-speed steel or P10 and P01 carbide.; John Wilkinson was the person who invented first boring machine tool in 1775.; Definition of Boring …
اقرأ المزيدThis operation may be performed in a drilling machine to finish a hardened hole. The grinding wheel is made to revolve with the spindle and is fed up and down. A suitable grinding wheel may be selected for surface grinding operation. Grinding can also be done to correct out of roundness of the hole. The accuracy in grinding operation is …
اقرأ المزيدGrinding wheels, maintenance, coolant, and grinding variables vary based on the operation.Cylindrical grinding is a common operation performed to finish parts and bring them to tolerance. A cylindrical grinder operator must be familiar with the machine itself, as well as how to select and utilize wheels, workholding, and coolant, in order for ...
اقرأ المزيدA surface grinder is a machine tool used to provide precision ground surfaces, either to a critical size or for the surface finish. The typical precision of a surface grinder depends on the type and usage, however ±0.002 mm (±0.0001 in) should be achievable on most surface grinders. The machine consists of a table that traverses both ...
اقرأ المزيدCenterless grinding operates on the principle of removing material from a workpiece without the need for a center point. It involves a centerless grinding machine with two grinding wheels, one fixed and the other adjustable. The workpiece is placed between these wheels, and the adjustable wheel, known as the regulating wheel, exerts …
اقرأ المزيد