Effect of Ball Milling Parameters on the Refinement …
Both Oda and Ameyama selected a low milling speed of 200 rpm and small. BPR (3.6:1 and 10:1) in their refinement process [21, ... the total mass of the milling ball and tungsten powder).
اقرأ المزيد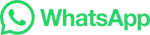