Typical cement manufacturing process flow diagram [4].
The flow diagram of a typical cement manufacturing process is shown in Fig. 1 [3]. Finally produced cement is transported in bags (packages) or as a bulk powder. ...
اقرأ المزيد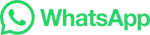
The flow diagram of a typical cement manufacturing process is shown in Fig. 1 [3]. Finally produced cement is transported in bags (packages) or as a bulk powder. ...
اقرأ المزيدProcess flow diagram for the cement manufacturing process, showing energy and heat consumption or inputs, as well as gaseous and particulate emissions (adapted from Ref. [31]). Note that emissions at the preheating and kiln stages include both fugitive emissions and cement kiln dust or those particulates captured with controlled …
اقرأ المزيدKnowing density of cement, the weight of the cement required to make a cement bed of 0.475 porosity can be calculated. Pass the air slowly through the cement bed at a constant velocity. Adjust the air flow such that the difference in h 1 of manometer and h 2 of flow meter maintains the constant value of h 1 /h 2. 38
اقرأ المزيدThe hydration of cement is an exothermic process. This means that a considerable amount of heat is evolved in this chemical reaction, which is termed as the heat of hydration. This heat surges the …
اقرأ المزيدGrinding. Cooled clinkers are ground to fine powder in ball mills. At final stages of grounding about 2-3% of powdered gypsum is added. (This is to avoid setting of cement quickly when it comes in contact with water) • Gypsum acts as a …
اقرأ المزيدIn this study the process flow diagram for the cement production was simulated using Aspen HYSYS 8.8 software to achieve high energy optimization and optimum cement flow rate by varying the flow rate of calcium oxide and silica in the clinker feed. Central composite Design (C.C.D) of Response Surface Methodology was used to …
اقرأ المزيدPart One: Raw Material Preparation. General. The production of cement is started from quarrying the raw material. The main raw materials are limestone, basalt, sand stone, pumice, gypsum. Site Exploration of suitable deposits, for the raw material has three main aims:-. Verifying the quality of the raw materials.
اقرأ المزيدCement Manufacturing – Process Modeling and Techno-Economic Assessment (TEA) using SuperPro Designer. This is the ReadMe file of a SuperPro Designer example that simulates a cement manufacturing ...
اقرأ المزيدFigure 11.12-1 is a generalized process diagram for concrete batching. The raw materials can be delivered to a plant by rail, truck or barge. The cement is transferred to elevated storage silos pneumatically or by bucket elevator. The sand and coarse aggregate are transferred to elevated bins by front end loader, clam shell crane, belt conveyor ...
اقرأ المزيدIt was observed that the control M40 concrete mix achieved a total embodied carbon of 482.88 kgCO2/m³. With 5 to 15% ESP of 100 µm fineness, the total embodied carbon was successfully reduced ...
اقرأ المزيدDownload scientific diagram | Flow chart showing the different stages in cement hydration, and admixtures action. from publication: Effect of a Carboxylic Acid on Rheological Properties of a High ...
اقرأ المزيدFLOWCHART 1. Convert the following flow chart into a paragraph of about 150 words. The process of making cement is described in this flow chart. The two raw materials used in theprocess are limestone and clay. Limestone is crushed, sized, dried and stored in storage silos. In the same way, Clay is washed, crushed, and dried in storage basins.
اقرأ المزيدThe cement industry is one of the most intensive energy consumers in the industrial sectors. The energy consumption represents 40% to 60% of production cost. Additionally, the cement industry contributes around 5% to 8% of all man-made CO2 emissions. Physiochemical and thermochemical reactions involved in …
اقرأ المزيدThe results show that approximately 2.48 t, 4.69 t, and 3.41 t of materials are required to produce a ton of the product in raw material preparation, clinker production, and cement grinding stages, and their waste rates are 63.31%, 74.12%, and 78.89%, respectively. ... mass flow diagrams for the input and output materials and flows in the ...
اقرأ المزيدEven if cement is a well-consolidated material, the chemistry of cement (and the chemistry inside cement) remains very complex and still non-obvious. What is sure is that the hydration mechanism plays a pivotal role in the development of cements with specific final chemical compositions, mechanical properties, and porosities. This …
اقرأ المزيد1.1.1.Chemical requirements for Portland Cement 1.1.2.Cement types 1.1.3.Clinker compounds 1.2. Typical raw materials used for cement manufacture 1.2.1.Limestones …
اقرأ المزيدProcess flow chart. The process flow chart is one of the most important outputs from process design and development. This is a complete flow chart of the process flow and can be used to identify sources of variation using cause and effect charts) for the complete process. A process flow chart means that the team can look at the complete process ...
اقرأ المزيدThe carbonation curing process parameters varied, including initial curing duration, carbonation curing duration, and carbonation pressure. Research findings showed that a maximum CO2 uptake of 12 ...
اقرأ المزيدFor a standard process, there are several licensors like UOP, Axens, Lummus, etc. & they are responsible for developing the PFD. Process flow diagrams of open art process units like CDU (Crude distillation unit), and VDU (vacuum distillation unit) can be found in the literature and encyclopedia of chemical technology.
اقرأ المزيدTYPICAL COMPOUND COMPOSITION OF ORDINARY PORTLAND CEMENT. CHEMICAL NAME CHEMICAL CEMENT WEIGHT. FORMULA NOTATION. …
اقرأ المزيدAs can be seen in Fig 1 (Process and Quality flow diagram) above, there are around 8 quality check points where by different samples are taken at some time interval (every hour most of the time) to check whether the raw materials/intermediate ... This procedure is used in the chemical analysis of cement, clinker, free-lime, and
اقرأ المزيدA block flow diagram (BFD) is a drawing of a chemical processes used to simplify and understand the basic structure of a system. A BFD is the simplest form of the flow diagrams used in industry. Blocks in a BFD can represent anything from a single piece of equipment to an entire plant. For a complex process, block flow diagrams can be …
اقرأ المزيدThe series of chemical reactions between calcium and silicon dioxide compounds form the primary constituents of cement i.e., calcium silicate. ... After explaining the complete process of cement making, flow …
اقرأ المزيدProcess flow diagram for portland cement manufacturing. 11.6-4 EMISSION FACTORS 11/21 Table 11.6-1. Source Classification Code (SCC) for Portland Cement …
اقرأ المزيد160+ million publication pages. 2.3+ billion citations. Download scientific diagram | Process flow diagram for the cement manufacturing process, showing electricity and heat consumption or inputs ...
اقرأ المزيدCement manufacturing is the source of 5% of global CO 2 emissions. 60% of emissions are due to the transformation of raw materials at high temperatures and 40% results from the …
اقرأ المزيدThe production process of the Portland cement is presented in Fig.1. The clinker, base component of the Portland cement, is obtained from the grinding, homogenization and subsequent burn in high ...
اقرأ المزيد1. The basics of cement manufacture – 2. History of cement manufacture – 3. Portland cement in today's world 2. Raw materials management system – 22. Concrete problems 16 1. Raw materials – 2. Raw mix – 3. Reserves – 4. Crushing – 5. Drying – 6. Pre-blending – 7. Storage and handling 3. Raw milling and blending 3.
اقرأ المزيدThe entire process flow diagram of the cement manufacturing pro cess is given by Figure 2 [3]. ... Those are fineness, water-cement ratio, chemical content, and admixtures. ... [Show full abstract
اقرأ المزيدCement manufacturing is a complex process that begins with mining and then grinding raw materials that include limestone and clay, to a fine powder, called raw meal, which is then heated to a sintering temperature as high as 1450 °C in a cement kiln. In this process, the chemical bonds of the raw materials are broken down and then they …
اقرأ المزيد