How to Choose the Correct GRINDING MEDIA
DIFFERENT MILLS REQUIRE DIFFERENT AMOUNTS OF MEDIA •BASED UPON WORKING VOLUME OR TOTAL VOLUME •Mills such as the Immersion Mill have a fixed amount determined by size of the basket •Steel Ball Mill 33.3% •Open Head Sand Mill 35-45% •Ceramic & Pebble Ball Mill 50% •Dry Grind Batch Attritor 45-60% •Wet Grind …
اقرأ المزيد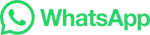