Development of a hydrometallurgical process for the recovery …
In order to recover pure alumina and synthesize magnesium spinel from black dross, a hydrometallurgical process was developed. This process consisted of 1) NaOH leaching of the mechanically activated black dross, 2) removal of silicate(IV) from the leaching solution by adsorption followed by coagulation, 3) precipitation of aluminum …
اقرأ المزيد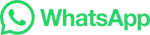