Design and simulation of gear box for stone crushing ball mill
During this stage the gear box plays a crucial role in terms of controlling speed and torque. The gear box is a collection of shafts, bearings, casing and gears in a systematic form to obtain the desired output. The operating load in the ball mill is 200 kN, critical speeds range from 343 rpm and a power of 12.4 kW. 1.
اقرأ المزيد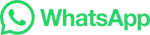