Wet and dry grinding of coal in a laboratory-scale ball mill: …
Although abovementioned authors [7,8,9,10,11,12,13,14,15] have pointed out many factors (mill speed, ball size, filling rate, feed size distribution, pulp density, coal …
اقرأ المزيد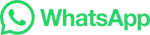
Although abovementioned authors [7,8,9,10,11,12,13,14,15] have pointed out many factors (mill speed, ball size, filling rate, feed size distribution, pulp density, coal …
اقرأ المزيدwhere d b.max is the maximum size of feed (mm); σ is compression strength (MPa); E is modulus of elasticity (MPa); ρb is density of material of balls (kg/m 3); D is inner diameter of the mill body (m).. Generally, a maximum allowed ball size is situated in the range from D /18 to D/24.. The degree of filling the mill with balls also influences productivity of the mill …
اقرأ المزيدParticle Size Analysis Methods: Typical Particle Size Rangers: Sieve Analysis: Dry sieving; Wet sieving; Air jet sieving; 40 μm—125 mm 20 μm—20 mm 10 μm—0.2 mm: Static Image Analysis (SIA) 0.5 μm—1.5 mm: Dynamic Image Analysis (DIA) 1 μm—30 mm: Static Light Scattering (SLS) or Laser Diffraction (LD) 10 nm—4 mm: Dynamic Light ...
اقرأ المزيدBased on his work, this formula can be derived for ball diameter sizing and selection: Dm <= 6 (log dk) * d^0.5 where D m = the diameter of the single-sized balls in mm.d = the diameter of the largest chunks of ore in the mill feed in mm. dk = the P90 or fineness of the finished product in microns (um)with this the finished product is ...
اقرأ المزيدThe 30 mm ball diameter milling still performed better than the small ball diameters, but the performance for this ball size had decreased for the -2 mm +1.4 mm mono-size feed …
اقرأ المزيدDOI: 10.1016/j.powtec.2019.09.062 Corpus ID: 208764858; Wet and dry grinding of coal in a laboratory-scale ball mill: Particle-size distributions @article{Bu2020WetAD, title={Wet and dry grinding of coal in a laboratory-scale ball mill: Particle-size distributions}, author={Xiangning Bu and Yuran Chen and Guangxi Ma and Yujin Sun and Chao Ni and …
اقرأ المزيدThe Planetary Ball Mill PM 100 is a powerful benchtop model with a single grinding station and an easy-to-use counterweight which compensates masses up to 8 kg. It allows for grinding up to 220 ml sample material per batch. The extremely high centrifugal forces of Planetary Ball Mills result in very high pulverization energy and therefore short ...
اقرأ المزيدThe particle size distribution of grinding products under different grinding conditions could be predicted by Eq. (17). This equation attempts to investigate this subject and describes a simple procedure for simulating the evolution behavior of the particle size distribution under different energy consumption for stirred mills.
اقرأ المزيدParticle size infl uences many properties of particulate materials and is a valuable indicator of quality and performance. This is true for powders, suspensions, emulsions, and aerosols. The size and shape of powders infl uences fl ow and compaction properties. Larger, more spherical particles will typically fl ow more easily than smaller or ...
اقرأ المزيدIn this study, we investigate the effect of the ball size in a high-energy ball mill on the comminution rate and particle size reduction. High-energy ball milling at 2000 rpm produces ultrafine talc particles with …
اقرأ المزيدDry ball milling requires less energy than wet ball milling but has a lower throughput. Wet ball milling requires more energy than dry ball milling but also has higher throughput. . Dry ball milling is more efficient for materials that don't require very fine particles or have a low tendency to group together.
اقرأ المزيدThe ball size distribution (BSD) in a mill is usually not known, as the measurement of the charge size distribution requires dumping the load and laboriously grading the balls into size classes. Fortunately we had one set of data as discussed below. The general non-availability of BSD necessitates the use of ball wear theory to estimate …
اقرأ المزيدBall Mill Power Calculation Example #1. A wet grinding ball mill in closed circuit is to be fed 100 TPH of a material with a work index of 15 and a size distribution of 80% passing ¼ inch (6350 microns). The required product size distribution is to be 80% passing 100 mesh (149 microns).
اقرأ المزيدA Results of particle size analysis 82 A.1 Batch grinding tests on single ball sizes 82 A.1.1 Particle size distributions obtained using 30.6 mm balls 82 A.1.2 Particle size …
اقرأ المزيدBall mill. Rod mill. Leave in the default option, Gyratory. ... Additionally, can be displayed graphically the inlet and outlet solids distribution to observe the change in particle size. 9.6 Solids Handling Example. 9.6.1 General Aspects. ... In …
اقرأ المزيدOver time, the metallurgical coke breakage in 4.0 cm balls presents significant variation with undergrinding for 0.5-1 min and overgrinding to grinding time from 3-10 min; 4.00 cm grinding media ...
اقرأ المزيدTo meet these two requirements, researchers have focused on two tasks. ... such as the mill speed, ball load, particle load, and ball diameter [4,5,6,7,8,9,10,11]. ... For the ball milling operation, the influence of particle size distribution on the grinding kinetics is also well-known now [8, 14, 23, 24, 34, 35]. Attention should be paid to ...
اقرأ المزيدThe type and concentration of stabilizer used have been found to strongly influence the particle size and size reduction kinetics of the nanosuspension produced 39, 45.Ito et al. [46] studied the effect of polymer species and concentration on the production of mefenamic acid nanosuspensions and reported that there is a relationship between …
اقرأ المزيدAfter 2 h of wet ball milling, the medians of the particle size distribution curves by volume and by number could be reduced from about 6 and 2 μm to about 1 μm and 70 nm, respectively ...
اقرأ المزيدbetween the feed particle size and the grinding media size match. These play a major role as gradation of media is influenced mostly by particle size and product fineness …
اقرأ المزيدThe effect of ball size on the particle size reduction has been investigated first for varying rotation speed of the container. Percent passing and size distributions of the milled Al 2 O 3 powder are shown in Fig. 1, Fig. 2, respectively, as a function of particle size for varying ball size.The average particle sizes (d 50) of the milled Al 2 O 3 powder are …
اقرأ المزيدThe iron mineral of the feed material was mainly magnetite and the gangue mineral was quartz. Fig. 1 shows that the PSD of the feed material (analyzed by a Malvern 3000 laser particle size analyzer, Malvern Panalytical, United Kingdom), which has a median particle size x 50 of 77.40 μm as well as an x 90 of 169.00 μm.
اقرأ المزيدTraditional ball mills and vertical mills are generally limited to a finished particle size of approximately 5 microns, which can be achieved only with great attention to media size. Grinding media for ball mills ranges in size from 6 - 10 mm for most traditional applications and 1.5 - 2.0 mm for vertical mills.
اقرأ المزيدThe effect of particle size distribution of wet ball mill products on low intensity magnetic separator. September 2020; ... The particle size distribution behavior (i.e., cumulative passing ...
اقرأ المزيدThe grinding machine was a laboratory scale mill made of alumina with an inside diameter of 0.13 m and an inner volume of 2.0 dm 3.The grinding media were alumina balls of 3600 kg m −3 density and two different ball diameters; 10 mm and 20 mm. The feed size of the material was 1180–1000 μm for all grinding conditions.The masses of the feed …
اقرأ المزيدEFFECT OF PARTICLE SIZE DISTRIBUTION ON GRINDING KINETICS IN DRY AND WET BALL MILLING OPERATIONS . ... Malghan ground a 8/10 mesh size fraction of …
اقرأ المزيدFig. 2 depicts the cumulative particle size curves for the wet and dry grinding under different grinding times. As the grinding time increased from 1 min to 10 min, the dry grinding indicated a faster reduction of the average particle size (d 50) compared to the …
اقرأ المزيدa) Particle size distribution (Dv10, Dv50, and Dv90) of LLZTO particles before and after high-energy ball milling in different solvents with 0.1–0.2 mm YSZ beads for 60 min. b) Average Dv50 values of LLZTO particles after high-energy ball milling in acetonitrile/Triton X-100 (0.1 wt%) for different time durations using two different YSZ …
اقرأ المزيدFollowing wet grinding, the particle size distribution is far more constrained than that in a dry setting. ... Ball mills have high energy requirements, and the efficiency …
اقرأ المزيدball mill grinding and particle size distribution ... appendix b.1 particle size distribution data and sized emission factors for selected sources 10/86 (reformatted 1/95) appendix b.1 b.1-1 ... Mills: Wet Grinding manufacturers, service companies and distributors are listed in this trusted and comprehensive vertical portal. The …
اقرأ المزيد