Sulfide Mineral Flotation Beneficiation Methods And Flow
Sulfide ore beneficiation is a major challenge for the mining industry. Recovery of valuable minerals such as copper, lead-zinc or nickel from sulfide-bearing ores requires complex and costly processes with a wide range of potential risks. These challenges can include the presence of harmful gases such as hydrogen sulfide and …
اقرأ المزيد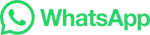