Analysis of Grinding Surface Creation by Single-Grit Approach
This paper presents some new research findings in the investigation of single-grit grinding in terms of surface creation. The investigation demonstrated that …
اقرأ المزيد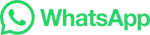
This paper presents some new research findings in the investigation of single-grit grinding in terms of surface creation. The investigation demonstrated that …
اقرأ المزيدUpdated: February 26, 2024 Published: November 16, 2023. In the realm of precision grinding, the choice of grit size in diamond and CBN (Cubic Boron Nitride) …
اقرأ المزيدThe grinding efficiency is analysed by considering the rubbing, ploughing and cutting of a single-grit grinding. By analysing the features of acoustic emission in single-grit grinding tests, an evidence-based scientific foundation has been established for monitoring grinding efficiency using acoustic emission.
اقرأ المزيدCarbon fiber-reinforced Polyether Ether Ketone is widely used in aerospace and medical industries due to its unique mechanical and physical properties. The use of CFR-PEEK in the industry is growing by replacing materials such as aluminum (in aerospace and mechanical industry), titanium, and stainless steel (in the medical …
اقرأ المزيدCBN grinding wheels offer several advantages when it comes to grinding ball bearings: High Hardness: CBN is one of the hardest materials available, which allows for efficient grinding of hardened ...
اقرأ المزيدThe material being ground also helps us determine the grit size. For hard to grind materials, we would recommend a finer grit size because a smaller particle will penetrate hard materials and form a chip easier than a larger blockier one. Difficult or hard to grind materials are abusive to the abrasive grain and can cause them to blunt or dull.
اقرأ المزيدDust control is an essential but time-consuming part of grinding concrete. Let's look at an example to get an idea of how some of those variables play out and look at the questions of time and slab size. Using a Husqvarna PG 820 RC, a 32" grinder (mentioned above), it's common to grind 7,000 to 10,000 square feet per day.
اقرأ المزيدkenya grinding of grit aggregates in production - Grinding Of Grit Aggregates In Production. Grinding wheels are available in a multitude of sizes, diameters, thicknesses, grit sizes and bonds. Abrasives are measured in grit or particle size and range from 8-24 grit (coarse), 30-60 (medium), 70-180 (fine) and 220-1,200 (very fine).News Detail.
اقرأ المزيدThis work focuses on the computational bridging between the meso- and macro-scale in the context of the hybrid modelling of Internal Traverse Grinding with electro-plated cBN wheels, and incorporates a regression analysis scheme to approximate the influence of the several cutting mechanisms on the meso-scale and to transfer the homogenisation …
اقرأ المزيدgrinding of grit aggregates in production rgeneralroof. a 16 grit concrete grinding pad label Pacific Grinding Concrete Polishing The use of 16 or 30grit size diamonds then use 60/80grit diamonds followed by the 120grit metal bond Mar 07, 2013 Process flow sheets: Paint, Varnishes and Pigments Production The main raw materials used in the ...
اقرأ المزيدGrinding wheel grit size has a direct effect on surface finish. The larger the grit size, the coarser the finish. It is important to select the correct grit size based on the finish requirements of the workpiece. Table 3 shows grit types, sizes and suggestions for various finish requirements. Before making …
اقرأ المزيدA grinding wheel is a wheel composed ... Today most grinding wheels are artificial composites made with ...grinding of grit aggregates in production. Friable grit breaks down more easily and is useful for cutting harder materials Grit size Grit size typically runs from coarse 16 24 grit medium 36 60 grit and fine 80 120 grit Superfine grits run ...
اقرأ المزيدIt is capable of processing a wide array of materials down to D97 = 20 µm. In the production of Carbon Black, the Mikro ACM reduces the carbon black's particle size, resulting in a lower grit size. Vertical Long-Gap Mill. The Vertical Long-Gap Mill is a grinding mill with an air classifier, and a specialized grinding chamber. This grinding ...
اقرأ المزيدGrit cutting depth model for wafer rotational grinding is established by calculating the material removal area based on two equivalent approaches: the kinematic relation in rotational grinding (macroscale approach) and the cutting area of effective grits (microscale approach), as shown in Fig. 1.In the macroscale approach, theoretical area …
اقرأ المزيدHard, brittle materials generally require a wheel with a fine grit size and a softer grade. Hard materials resist the penetration of abrasive grains and cause them to dull quickly. Therefore, the combination of finer grit and softer grade lets abrasive grains break away as they become dull, exposing fresh, sharp cutting points.
اقرأ المزيدHowever, in the case of smaller fractions (4–8 mm), the impact of the crushing process on the value of the crushing strength indicator is smaller, and, thus, the strength properties of the aggregates (gravel and grit) are less important than in case of the grits obtained as a result of crushing (fraction 10–14 mm).
اقرأ المزيدProper grinding wheel selection is essential to ensure that the required part quality, production rate, and overall cost per part is achieved. Although the type of abrasive grain is often a primary driver of wheel …
اقرأ المزيدThe process of grinding consists of many factors, for example, the size and form of crushed grains, as well as their mutual arrangement inside the crushing machine …
اقرأ المزيدKEY TAKEAWAYS. To make exposed aggregate concrete smooth: Use a broom and a mix of floor cleaner with warm water to remove debris. Level the rough patches with a hammer and chisel. Apply epoxy …
اقرأ المزيدFour different designs of grinding wheels were fabricated using the DLP additive manufacturing process. These designs were based on various cooling strategies, including a solid structure with regular external cooling (SS), a structure with cylindrical internal cooling channels (CP) with a 1.5 % reduction in the active surface compared with …
اقرأ المزيدCreating scratch by an abrasive grit is mostly investigated to enhance the finishing processes. The grinding process is such that a number of abrasives with a specific statistical distribution is engaged with the workpiece and performs the material removal. If we can consider the scratching and material removal processes for a single grit …
اقرأ المزيدAutomotive transmission gears are ground via novel process performed without lubricants. A threshold grinding energy level is defined, below which grinding burns are avoided. Geometric accuracy of the dry-ground gears is verified. Process parameters are optimized via a DOE technique. Process parameters are realistic for immediate …
اقرأ المزيدIt is processed by the abrasive grit industry in grit sizes of 1 to 1100 μm grit diameter. Natural diamond is primarily used for grinding and slicing glass, ceramic products, and …
اقرأ المزيدDental grinding is a material removal process based on the interactions of multiple grits and materials. To simulate the dental grinding process, the schematic illustration of the bur-specimen interactions in dental machining is given in Fig. 1.During grinding, the bur rotated at a rotational speed, shifted along the machining surface at a …
اقرأ المزيدSome Avian Vets Find That A Pinch Of Grit, Gravel Per Month Will Help With The Grinding Process. On the other side of the spectrum, there are avian vets who advocate a moderate use of grit or gravel for budgies. They suggest that a small quantity, approximately a pinch, per month can aid the budgies' digestive process.
اقرأ المزيدGrinding is usually used to increase the specific surface area of steel slag to improve its activity. However, due to the large amount of hard-to-grind minerals in steel slag, a large amount of energy is wasted in the grinding process. Therefore, the current investigation aims to remove the hard-to-grind minerals in steel slag as much as possible …
اقرأ المزيدmachining process for large scale production. Typically, grinding is performed as a finishing unit process at the end of process chains to improve surface quality and dimensional accuracy. For hard-to-machine materials, it can also be the major shaping process. In grinding, abrasive grit particles are held in a bonding
اقرأ المزيدAt low grinding wheel speeds or very high feed rates, the overlapping of single grit paths enables the production of deterministic structures on the workpiece. ... Another special application of wheels with defined grit patterns is grinding of brittle materials in ductile mode [88, 271]. The idea is to use coarse grits that are dressed to a ...
اقرأ المزيدGrinding Wheel. In the grinding process, an emery or corundum wheel is used as the cutting tool. Emery and corundum are naturally found abrasives and are impure forms of aluminium oxide Al 2 O 3.A grinding wheel is made up of thousands of tiny abrasive particles embedded in a matrix called the 'bond' An abrasive is an extremely …
اقرأ المزيدThe abrasive used for each succeeding grinding operation should be one or two grit sizes smaller than that used in the preceding step. A satisfactory fine grinding sequence might involve SiC papers with grit sizes of 240, 320, 400, and 600 grit [P280, P400, P800 and P1200]. This sequence is used in the "traditional" approach.
اقرأ المزيد