Efficiency of the Use of High-Quality Grinding Balls from
Abstract The results of industrial comparative tests of batches of grinding balls with a diameter of 40, 60, and 80 mm from chromium–molybdenum steel of the nominal grade ShKhM and balls of the current manufacture from rail steel in the first chambers of drum mills while grinding of cement are presented. As the test results …
اقرأ المزيد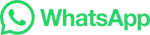