Modelling of the High-Energy Ball Milling Process
High-energy ball milling is a complicated process employed in solid reactions for obtaining nanostructured materials, in powder form, with an average particle size of less than 100 …
اقرأ المزيد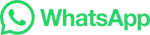
High-energy ball milling is a complicated process employed in solid reactions for obtaining nanostructured materials, in powder form, with an average particle size of less than 100 …
اقرأ المزيدThe Wet Ball Mill system consists of Wet Ball Mill, Wet Ball Mill Lubrication system, Mill circuit tank with an agitator, Mill circuit Pump, Mill Hydro cyclone, 3-way distributor and accessories. The Wet Ball Mill is the wet horizontal type. The Process water is supplied to Wet Ball Mill and Wet Mill circuit Tank. Slurry from the …
اقرأ المزيدThe Rainhart Aggregate Wet Ball Mill is used to determine the resistance of aggregate in flexible base materials to disintegration in the presence of water. These results are …
اقرأ المزيدpirical formulae for wet rod mills and wet and dry ball mills, where the diameter occurs as DO.4. The formula contains in accordance with above explana tion - the factor Os …
اقرأ المزيدIf so, maybe plunge milling (also called plunge roughing) is the answer. Let's start by taking a look at what plunge milling is. The idea, is to rough out a pocket, profile, or 3D …
اقرأ المزيدWet Batch Laboratory Mills Wet Circulation Laboratory MillsChocolate Grinding Attrition MillsLimestone Grinding Ball Mill (CL)Limestone Slaker Ball Mill (CLS)Small Media Bead Mills (SDM) Skip to content 330.929.3333. Mixing Tanks; Other Products & Services.
اقرأ المزيدBall filling and mill fractional speed were kept constant respectively at 20% and 60% while slurry filling was varied from 0% to 300%. Using a high speed video camera, the motion of the charge was captured. The movies were then analysed frame by frame and the angular positions of the media shoulder, the media toe as well as the pool of slurry ...
اقرأ المزيدThe entire mill feed enters the drum via a chute or spout and an internal spiral carries the feed into the trunnion liner. The drum feeder may be used in lieu of a spout feeder when headroom limits direct spouting. The drum also provides a convenient method of adding grinding balls to a ball mill. The drum is generally lined with Manganese Steel.
اقرأ المزيدIn order to determine the influence of milling parameters on the kinetics of MA, ball milling of +300 mesh size, elemental Fe powder and a powder blend of nominal composition (expressed in atomic percentage) Cu 82 Al 18 has been performed in a Fritsch Pulverisette P5 planetary ball mill with individual constituents having a purity level of …
اقرأ المزيدAn experimental vibratory mill using angular oscillations was used for this study (Franchuk, 1970, pp. 193–197; Janovich, 2015) but theoretical investigations to understand the process were carried out here. ... Ball mill simulation in wet grinding using a tumbling mill and its correlation to grinding rate. Powder Technology ... Ball-milling ...
اقرأ المزيدal. [17] developed a mechanistic model in plunge milling of cylindrical parts with a multi-blade cutter. Zhuang et al. [18] analyzed the cutting zone between two adjacent posi-tions of plunge milling and calculated the dynamic cutting width at a given angular position. A mechanistic model of three-axis plunge milling was then established to predict
اقرأ المزيدThe experimental results show encouraging accuracy to apply this approach to recognize the wet ball mill's load, with a recognition rate of 98.67%. ... Angular oscillation model to predict the performance of a vibratory ball mill for the fine grinding of grain. Biosystems Engineering, Volume 171, 2018, pp. 155-164.
اقرأ المزيدNETZSCH Ecutec's Taurus has the most advanced technology in Mills using Grinding Media for micronizing. A rotating robust steel drum with liners is supplying kinetic energy to grinding media inside the mill. These grinding media are crushing and grinding fresh product due to impact and friction. The lining as well as the grinding media can be ...
اقرأ المزيدMill Type Overview. Three types of mill design are common. The Overflow Discharge mill is best suited for fine grinding to 75 – 106 microns.; The Diaphram or Grate Discharge mill keeps coarse particles within the mill for additional grinding and typically used for grinds to 150 – 250 microns.; The Center-Periphery Discharge mill has feed reporting from both …
اقرأ المزيد22 May, 2019. The ball mill consists of a metal cylinder and a ball. The working principle is that when the cylinder is rotated, the grinding body (ball) and the object to be polished (material) installed in the cylinder are rotated by the cylinder under the action of friction and centrifugal force. At a certain height, it will automatically ...
اقرأ المزيدThe idea, is to rough out a pocket, profile, or 3D surface by plunging either a twist drill, an end mill, or a special-purpose tool straight down into the material. Here's a typical example: The graphic shows a typical plunge milling operation for a square pocket, courtesy of BobCAD. As you can see, a chain of holes are plunged vertically ...
اقرأ المزيدIf a ball mill uses little or no water during grinding, it is a 'dry' mill. If a ball mill uses water during grinding, it is a 'wet' mill. A typical ball mill will have a drum length that is 1 or 1.5 times the drum diameter. Ball mills with a drum length to diameter ratio greater than 1.5 are referred to as tube mills.
اقرأ المزيدTrying to plunge with a ball nose will be pretty tough.. Determining factors may be material and if you have a start hole already A sharp endmill will indeed break …
اقرأ المزيدA single angle cutter is designed for milling dovetails, chamfering or beveling parts and manufactured in single right and left angles at 45° & 60°. Double or equal angle cutters have v-shaped teeth with both conical surfaces at an angle to the end faces, used for milling threads, v-grooves, serrations, and other angular surfaces.
اقرأ المزيدThis really comes into play if you need to work with small bits (< 3mm) to keep from breaking them. Of course, if you need a flat surface, a flat end mill will give better results. One strategy is to rough cut with ball nose and finish with flat. I consider the up cut ball nose, and it's cousin the bull nose, the first choice for removing material.
اقرأ المزيدTo overcome the difficulty of accurately judging the load state of a wet ball mill during the grinding process, a method of mill load identification based on the singular value entropy of the modified ensemble empirical mode decomposition (MEEMD) and a probabilistic neural network (PNN) classifier is proposed. First, the MEEMD algorithm is …
اقرأ المزيدAngular oscillation model to predict the performance of a vibratory ball mill for the fine grinding of grain - ScienceDirect. Biosystems Engineering. Volume 171, July …
اقرأ المزيدAmong high-energy ball mills, the planetary is a mechanically simple and versatile device for efficient grinding. It is usually made of two or more jars, rotating at an angular velocity ω around their axis (see Fig. 1), installed on a disk rotating at angular velocity Ω.Grinding occurs by impact among the milling media (balls and jars), driven by …
اقرأ المزيدGrinding in ball mills is an important technological process applied to reduce the. size of particles which may have different nature and a wide diversity of physical, mechanical and chemical ...
اقرأ المزيدFigure 2.27. Cut-away view of the Hardinge conical ball mill showing how energy is proportioned to the work required is about 0.3 kg/Mg of material for dry grinding, and 1-1.5 kg/Mg for wet grinding. The normal charge of balls is about 5 Mg/m3. In small mills where very fine grinding is required, pebbles are often used in place of balls.
اقرأ المزيدPlanetary mill: In the planetary ball mill, the vessels are positioned on a spinning support disk in a planetary pump spinning on its axes (Guzzo et al., 2020). ...
اقرأ المزيدHowever, plunge milling process can exhibit a problem at the end of plunging phase, which is the increase of cutting forces. Within this paper, the study considers the case of wet plunge milling process applied to Ti-6Al−4 V alloy, that is the most generally used titanium alloy and applied in a wide range of applications.
اقرأ المزيد3.1 Effects of Ball Milling Velocity and Ball Volume Fraction. EDEM as a powerful software enables to collect data from the dynamic behavior of the entire ball milling simulation process. In order to explore the milling efficiency of the models, the average speed of balls, the maximum speed of balls, and the magnitude of torque on the …
اقرأ المزيدThe Rainhart Aggregate Wet Ball Mill is used to determine the resistance of aggregate in flexible base materials to disintegration in the presence of water. These results are essential in determining whether the base will resist crushing, degradation, disintegration, and premature structural failure.
اقرأ المزيدSchematic representation of a planetary ball-mill. Right, three-dimensional view; middle and left, definition of the jar radius R j and the distance between axis of rotation (angular velocity ω ...
اقرأ المزيد