Experimental study of clinker grinding in a ball mill and
Discrete Element Methods (DEM) is a numerical tool consolidated to the simulations of collisions in particulate systems. In this paper, the method was used to study the collisions between grinding media and grinding media and walls in ball mills, which is the most used unit operation in clinker grinding, the majority component of the cement. …
اقرأ المزيد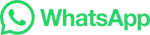