(PDF) Iron Ore Sintering: Process
Sintering is a thermal agglomeration process that is applied to a mixture of iron ore fines, recycled ironmaking products, fluxes, slag-forming agents and solid fuel (coke). The purpose of the ...
اقرأ المزيد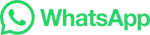
Sintering is a thermal agglomeration process that is applied to a mixture of iron ore fines, recycled ironmaking products, fluxes, slag-forming agents and solid fuel (coke). The purpose of the ...
اقرأ المزيدThe problem involved in Manganese Ore Processing deals with the production of acceptable specification grades of manganese concentrates at a maximum recovery of the total manganese from ores …
اقرأ المزيدPhase analysis. XRD pattern of the Mn-ferrite synthesized from low grade Mn-ore at different sintering temperatures (1000, 1100 and 1200 °C) is shown in Fig. …
اقرأ المزيدIntensification of the iron ore sintering process was approached by injecting hydrogen-rich gas into the sinter bed. ... In an industrial-scale sinter plant with a waste gas recycling arrangement, above 20%, productivity got adversely affected as oxygen in the recycled gas started dropping below 19%. The deficiency of oxygen has affected the ...
اقرأ المزيدDuring the sintering process, sinter fuels are commonly used to provide the required energy. The coke breeze comes from coking plant (typically less than 3 mm in size) and is widely used due to ...
اقرأ المزيدThe sinter production from concentrate of low-grade manganese ore for use in the production of ferrosilicomanganese was discussed. It was found that the chemical composition of the concentrate ...
اقرأ المزيدAn increasing proportion of fine ore and concentrate is being used in ferroalloy production. This has inspired studies to process these materials in a more economical, reliable and environmentally friendly way in the face of ever-toughening competition in the industry. A process for sintering manganese ore was developed by Outokumpu with equipment …
اقرأ المزيدThe problem involved in Manganese Ore Processing deals with the production of acceptable specification grades of manganese concentrates at a maximum recovery of the total manganese from ores having variable characteristics. The flowsheet provides for both gravity and flotation with a maximum recovery of the manganese …
اقرأ المزيدManganese Ore Beneficiation Plant (0.5 MTPA) ... ≥45% Mn sinter- alloy grade with 50% yield is included. ... jigging of -20+5 mm, classification with Stub cyclone of the screen under size [-5mm], Wet high intensity plate magnetic separation of sands, Wet medium- high intensity drum magnetic separation of slimes<0.2 mm which yielded a ...
اقرأ المزيدIn June 1976 a 600'tonne/day manganese ore sinter machine, with on-strand cooling, was commissioned at the plant of Tasmanian Electro Metallurgical Company Pty. Ltd. at Bell Bay, Tasmania. This machine was installed in order to utilize manganese lump ore screenings generated in the preparation of raw materials prior to charging to the electric …
اقرأ المزيد100 TPD or less) Manganese ore sinter plants -1) Khandelwal Ferro Alloys Ltd, 2) Chandrapur Ferro . Alloy Plant of SAIL (earlier known as Maharashtra Elektrosmelt Ltd) and 3) Navbharat Ferro Alloys .
اقرأ المزيدmanufacture of Manganese Ore Sinter on a continuous sinter plant of 20 Tons per day capacity. Introduction In the process of mining of ores, a lot of fines is generated. Similarly in operations such as crushing, screening. transporting Et stacking, a large quantity of fines is generated For smelting operation in furnace, raw materials in a
اقرأ المزيدTemperature control (/profile) important in drying and in sintering. Moisture / coke / cooling air circulation. Coke fines/dust required. Coal volatiles can block the bed or burn near steel belt. Pressure difference. In sintering lower than …
اقرأ المزيدIron ore fines, coke breeze, limestone and dolomite along with recycled metallurgical wastes are converted into agglomerated mass at the ... Sinter Plant, which forms 70-80% of iron bearing charge in the Blast Furnace. This entire process of sinter making is associated with various safety hazards like hit / entanglement with mobile equipment ...
اقرأ المزيدore upgrading, used by the most of ore producers. The performance of manganese ore sinter plants as well as a sinter quality depend strongly on the type and quality of ores used for its production[12,13] but even so there is not a lot of studies concerning manganese ores sintering in comparison with the iron ores sintering studies.
اقرأ المزيدMill scale is a valuable metallurgical raw material since it contains 65–70% iron. JSW Steel Ltd is a 7 Mtpa integrated steel plant and generates 270 t of mill scale per day. Most of the materials of steel plant wastes are recycled through sinter making in most of the countries…. View on Taylor & Francis. Save to Library.
اقرأ المزيدThe present work proposes a novel process to sinter porous iron ore (porosity ~23–24%) with enhanced productivity and quality. The iron ore is pre-processed in the presence of calcined lime for the temporary closure of pores, which further prevents water absorption during the granulation process in drum in the presence of water. The …
اقرأ المزيدThe metallic alloy produced at 1600 0 C and three hours of smelting with constant reductant/charged ore of 5% and 8% manganese ore addition was having concentrations of 54.52% Fe, 16.79% Cr, 4.92% ...
اقرأ المزيدmedium.This process was able to upgrade the manganese ore economically from 38 to 42 per cent manganese. At the end of 1989 a production dense-mediumseparation plant was commissioned, producing a 41,S per cent manganese feedstock for con sumption in the sinter plant. With the use ofthis material, the sinter plant produced a
اقرأ المزيدManganese and silicon are completely miscible in the liquid state. The minimum eutectic temperature at the Mn-rich side is 1038°C at X Si = 0.175 (11.2 wt% Si). Several silicides are formed during solidification (Fig. 7.5).Manganese silicide compositions (Gasik et al., 2009) have been updated—for instance, the MnSi 2 formula is being …
اقرأ المزيدThe main unit operations in the sinter process are the sizing of the ore to < 6 mm, the mixing of the ore with water and solid reductant to form the green sinter mix, and the ignition of the green ...
اقرأ المزيدAbstract. The use of sinter influences hot metal production substantially and significantly affects an integrated steel mill's total emissions. Sintering of iron ores is an enormous energy-intensive and resources consuming process. Introducing a selective waste gas recirculation (SWGR) to the sintering process reduces the energy consumption ...
اقرأ المزيدTemperature control (/profile) important in drying and in sintering. Moisture / coke / cooling air circulation. Coke fines/dust required. Coal volatiles can block the bed or burn near …
اقرأ المزيدIron ore sintering accounts for 13 % of CO 2 emissions. Pelletization and coke are making account for 7 % of the emissions. In the year 2022, about 222.1 kg CO 2 is discharged per ton sinter. Depending on operating conditions and plant output capacity, a sinter plant can release anywhere from 1500 to 2500 Nm 3 /t of gases in
اقرأ المزيدManganese ore is required in iron making to control the manganese content of the hot metal in the desired range. Unlike other plants, where manganese ore lump is used directly in blast furnace, in VSP, it was proposed to use manganese ore fines in sinter productions. This would ensure much more consistent manganese content in the hot metal.
اقرأ المزيدThe first plant was setup for iron ore fines, the second unit was setup for utilization of manganese ore fines and the third plant was setup for utilization of …
اقرأ المزيدan ore preparation facility and sinter beneficiation plant which will process the three million tons of ore to produce 2.4 million tons of a high grade sinter (44% Mn) per annum. Our product. We produce and sell sintered Manganese. At full production we expect to produce sintered Manganese of 44 – 46 % Mn quality grade. Our Infrastructure
اقرأ المزيدore upgrading, used by the most of ore producers. The performance of manganese ore sinter plants as well as a sinter quality depend strongly on the type and quality of ores …
اقرأ المزيدWastewater is generated mostly in sinter plants where multi-cyclone are used for cleaning process gas (Li et al. 2019b). ... Studies performed on iron ore sintering plants have indicated that PCDD/Fs are formed through a de novo synthesis, taking place in the sinter bed in regions where the temperature is 250–450 °C. ...
اقرأ المزيد