FLASH CALCINERS A focus on flash calcining
to assure that the small fraction of oversized material will be ground). • low thermal inertia due to the limited amount of refractory lining in the equipment, allowing for a faster start-up and production. • easy control philosophy, very similar to a calciner in a clinker kiln. • overall thermal energy consumption
اقرأ المزيد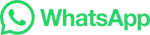