PM 400 Planetary Ball Mill | Glen Mills, Inc.
The extremely high centrifugal forces of planetary ball mills result in very high pulverization energy and therefore short grinding times. The PM 400 is a robust floor model with 4 grinding stations. You may also be interested in the High Energy Ball Mill Emax, an entirely new type of mill for high energy input.
اقرأ المزيد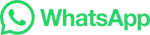