Crushing characteristics and performance evaluation of iron …
In this study, the crushing process of spherical iron ore particles, constructed by an Apollonian sphere packing (ASP) method, was numerically reproduced in a cone …
اقرأ المزيد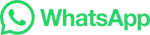
In this study, the crushing process of spherical iron ore particles, constructed by an Apollonian sphere packing (ASP) method, was numerically reproduced in a cone …
اقرأ المزيد1 Introduction. The effectiveness of simultaneous effect of mechanical load and electric field of ultra-high frequency (UHF) in the process of iron ore crushing is substantiated in …
اقرأ المزيدOnce the primary crushing stage is complete, the smaller iron ore pieces are further crushed using a secondary crusher. The secondary crusher reduces the size of the ore particles to 0.5-2 cm in ...
اقرأ المزيدMoving cone Diemeter (mm) HPY200. C. 13. 150. 120-240. 160. 950. F. 6. 76. 55-180. 160. ... 245-730. 630. 1800. Features & Benefits. Limestone crusher features and benefits: Effective Crushing: With a large crushing capacity, limestone crushers are made for the effective crushing of limestone and related minerals. ... Iron Ore Dryer. Stone Ball ...
اقرأ المزيدore crushing and the iron content in the grinding products. ... crusher implementing the effect of UHF electric field on each m ono lithic unit located . within its working space is proposed [7].
اقرأ المزيدExpert in Ore Crushing and Manufacturer of Ore Beneficiation Equipment. MoleDive assists the mining and sand and gravel industries (including gold, iron, copper, soft stone, granite, limestone, and more) in crushing, sorting, and grinding processes. Our equipment, including jaw crushers, impact crushers, cone crushers, double-roll crushers ...
اقرأ المزيدGyrating or cone crusher: It uses a repeated compression action with fixed and moving crushing members. This kind of crusher produces less than 20% fines, and the aggregates are rather of cubic form. ... A. Jankovic, in Iron Ore, 2015. 8.2.1. Crushers. Crushers are machines that use a rigid surface to compress and break large rocks into smaller ...
اقرأ المزيدThere are three main steps in designing a good crushing plant: process design, equipment selection, and layout. The first two are dictated by production requirements and design …
اقرأ المزيدThe crushers are built to perform with the lowest cost per ton, featuring a unique combination of crusher cavity design, crushing forces, reliability and safety. Engineered spare and wear parts as well as maintenance and optimization services are designed with decades of experience in different crushers and crushing processes.
اقرأ المزيدMcLanahan Mineral Sizers are designed to process a variety of materials, including copper, iron ore, gold, nickel, lithium/spodumene, coal, potash, phosphate and other hard rock and soft, non-coal minerals. They can be used in primary or secondary crushing applications. They excel at handling feeds with clays and other contaminants that are ...
اقرأ المزيدBlake jaw crushers, also as double toggle jaw crushers, are characterized by the position of the pivot of the swing jaw, which is located at the top of the machine. This design allows for a larger feed size and a higher capacity, making it suitable for primary crushing. The motion of the swing jaw in a Blake crusher is predominantly vertical ...
اقرأ المزيدIron ore pre-treatment equipment. The pre-treatment stage of iron ore mainly includes crushing, screening, grinding, and grading processes.. Crushing and screening: The raw ore is sent to the crusher by the vibrating feeder, and the crushed product enters the screening machine. The materials on the screening return to the crusher for further …
اقرأ المزيدThe raw material is extracted from the iron ore mine and transported to the primary crusher. This is where the initial crushing takes place, reducing the size of the ore into smaller pieces that can be handled more easily. Next, the crushed material is conveyed to secondary crushers for further processing.
اقرأ المزيدThe iron ore impact crusher utilizes a plate hammer on a high-speed moving rotor to produce a high-speed impact on the iron ore fed into the crushing chamber. The crushed iron ore is thrown at a high speed in the tangential direction toward the counter-attack at the other end of the crushing chamber.
اقرأ المزيدInnovation has an important role in improving the productivity, safety and sustainability of mining operations. Historically, ore transport was done by diesel trucks, but with the commitment to reduce CO2 emissions and increase mine safety, mining companies have invested in innovative, more sustainable ore transport technologies. The innovative …
اقرأ المزيدThis method treats ore strongly combined with non-ferrous rock. The crushed ore is put in a slurry of ferrosilicon (an alloy of iron and silicone) and due to the specific gravity of the slurry, low-density rock floats and the iron sinks. The End of Natural Ore. Hull-Rust production ceases in the early 1960s. Pioneer Mine sizing plant shut down ...
اقرأ المزيدIn a crusher's design, attention to the reduction ratio is critical. This ratio reflects the degree to which the material is reduced in size from the feed to the product. A high reduction ratio indicates a powerful crushing capacity, such as reducing 150-centimeter-wide iron ore to a 30-centimeter-wide material.
اقرأ المزيدFlexibility. For gravel: less crushing, more screening. For rock: crushing and screening. Crushing Ore. Maximum size reduction. Shape of no importance. Over and undersize of …
اقرأ المزيدIn this paper, the crushing process of spherical iron ore particles in a cone crusher has been numerically reproduced by DEM. The effects of operation parameters …
اقرأ المزيدRock Crusher History. History tells us, it was in 1830, the first US patent was issued on a rock crushing machine. It covered a device which, in a crude way, incorporated the drop hammer principle later used in the famous stamp mill, whose history is so intimately linked with that of the golden age of mining. In 1840, another patent was …
اقرأ المزيدThe first step of physical beneficiation is crushing and grinding the iron ore to its liberation size, the maximum size where individual particles of gangue are separated from the iron minerals. A flow sheet of a typical iron ore crushing and grinding circuit is shown in Figure 1.2.2 (based on Ref. [4]). This type of flow sheet is usually ...
اقرأ المزيدWe would like to show you a description here but the site won't allow us.
اقرأ المزيدThe iron ore impact crusher utilizes a plate hammer on a high-speed moving rotor to produce a high-speed impact on the iron ore fed into the crushing …
اقرأ المزيدThis is the second stage of crushing. Feed size, which is around 150 to 300 mm, of the rock or ore from the primary crushing process is reduced to between 50 and 80 mm. Tertiary Crushing. This is the third stage of crushing. The size, which is around 50–80 mm, of the ore or rock from the secondary crushing process is reduced to between 5 and ...
اقرأ المزيد5.1. A primary gyratory crusher was required to crush iron ore at the rate of 3000 t/h. The largest size of the run-of-mine ore was 1000 mm. The required product size was less than 162 mm. Manufacturer's data indicated that the nearest size of gyratory crusher would be 1370 mm × 1880 mm with a cone angle of 18°.
اقرأ المزيدFirst Online: 03 June 2023. 6 Accesses. Download reference work entry PDF. Measurement-control for crushing and screening process is the measurement and …
اقرأ المزيدA coal crusher is a machine designed to break large chunks of coal into smaller, more manageable pieces. It is a crushing device specifically engineered for the efficient reduction of high-moisture content coal, overcoming the challenges associated with traditional crushing methods. The coal crusher plays a crucial role in various industries ...
اقرأ المزيدcrusher's discharge opening, as the production continues through an on-line coarse size analysis of the crushed product (digital image analyses). Dance, A. 2001) • More attention is being paid to the impact on crushing circuit design caused by variations in ore characteristics, size distribution, moisture content, ore grade and climatic
اقرأ المزيدThe maximum crushing ratio of coarse crushing is about three. The main force in the coarse crushing of ore is crushing. Typical coarse crushing equipment includes jaw crusher, gyratory crusher, and roller-tooth crusher. Ore medium crushing is a process of crushing ore blocks with a feeding particle size of 125–400 mm to 50–100 …
اقرأ المزيدBayan Obo is rich in iron, rare earth, niobium and other metals. Iron is one of the main minerals here. Iron is harder than most stones. According to the traditional iron ore processing process, the jaw crusher is used for rough crushing, and the ore is subjected to primary rolling from large pieces to small pieces.
اقرأ المزيد