The cement mill
Cement manufacturing -brief description of a cement mill. Cement clinker is usually ground using a ball mill. This is essentially a large rotating drum containing grinding media - normally steel balls. As the drum rotates, the motion of the balls crushes the clinker. The drum rotates approximately once every couple of seconds.
اقرأ المزيد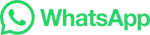