A Comprehensive Guide to Ball Mill Manual
A ball mill is a crucial piece of machinery used in grinding and mixing materials in various industries. It works by rotating a cylinder with steel or ceramic balls, causing the balls to fall back into the cylinder and onto the material to be ground. Ball mills are used extensively in the mining, construction, chemical, and pharmaceutical ...
اقرأ المزيد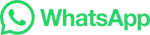