Crushing in Mineral Processing
In mineral processing or metallurgy, the first stage of comminution is crushing. Depending of the type of rock ( geometallurgy) to be crushed, there are 2 …
اقرأ المزيد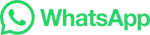
In mineral processing or metallurgy, the first stage of comminution is crushing. Depending of the type of rock ( geometallurgy) to be crushed, there are 2 …
اقرأ المزيد3. 3. Processing of Copper Ore. Top: Sulfide ore processing. Bottom: Oxide ore processing. The process varies slightly depending on the type of ore that is being mined. Sulfide ores are first put through a jaw or gyratory crusher to reduce the rocks to about 7 - 8 inches. This material is then fed to a secondary grinder that further reduces the ...
اقرأ المزيدComparative high pressure grinding rolls (HPGR) and cone crusher pilot-scale tests were conducted using Upper Group 2 (UG2) platinum-bearing ore in order to determine the impact of micro-cracks in HPGR products toward energy requirements in ball mills and the degree of liberation. The ball mill was fed with HPGR and cone crusher …
اقرأ المزيدCrushing is usually a dry process and carried out on ROM ore in succession of two or three stages, namely, by (1) ... ∼0.15 m 3 of 13 cm diameter iron or steel balls are added into the mill per 0.85 m 3 of ore (i.e., 15 vol.% "steel") to assist grinding. SAG mills are much more common. ...
اقرأ المزيدThe ore size reduction process involves two steps: crushing and grinding. The grinding process is the final operation of making the mineral to dissociate from the monomer and making the particle size …
اقرأ المزيدThe process of ball milling involves the grinding and mixing of metal particles within a ball mill, which is a type of equipment used for grinding, with the aim of producing a fine powder . This method has been widely employed in the manufacturing of metal powders from diverse sources, including metals, alloys, and intermetallic compounds.
اقرأ المزيدBall Mills. In all ore dressing and milling Operations, including flotation, cyanidation, gravity concentration, and amalgamation, the Working Principle is to crush and grind, often with rod mill or ball mill, the ore in order to liberate the minerals. In the chemical and process industries, grinding is an important step in preparing raw ...
اقرأ المزيدUse washing to remove very fine harmful particles. Washing of run-of-mine ore can be carried out to facilitate sorting by removing obscuring dirt from the surfaces of the ore particles. However, washing to remove very fine material, or slimes, of little or no value, is more important. Washing is normally performed after primary crushing as the ...
اقرأ المزيد4) Purification or refining of the metal (1) Crushing and Grinding of the Ore. The ores occur in nature as huge lumps. They are broken to small pieces with the help of crushers or grinders. These pieces are then reduced to fine powder with the help of a ball mill or stamp mill. This process is called pulverisation. (2) Concentration of Ore or ...
اقرأ المزيدExpert in Ore Crushing and Manufacturer of Ore Beneficiation Equipment. MoleDive assists the mining and sand and gravel industries (including gold, iron, copper, soft stone, granite, limestone, and more) in crushing, sorting, and grinding processes. Our equipment, including jaw crushers, impact crushers, cone crushers, double-roll crushers ...
اقرأ المزيدMost of the high-grade hematite iron ores are typically subjected to simple dry processes of crushing and classification to meet the size specifications required for direct shipping ore (DSO). This involves multistages of crushing and screening to obtain lump (−31.5 + 6.3 mm) and fines (approximately −6.3 mm) products.
اقرأ المزيدIntroduction. An iron ore mill relies on the grinding and impact of grinding balls to complete iron ore crushing. The operating process of an iron ore mill is as follows: …
اقرأ المزيدBall Grinding Process. Ball grinding process is a grinding method of crushing ore with ball-shaped grinding medium in the grinding mill. In the ball grinding …
اقرأ المزيدThe material to be ground is fed into the mill through the hollow shaft, and the grinding medium, usually steel balls, are put inside the cylinder. Ore Grinding Process: Crushing and Grinding: ...
اقرأ المزيدRelatively deep deposits, or those with elongated or irregular shapes are typically mined from underground with deep vertical shafts, declines (sloped tunnels) and levels (horizontal tunnels) (Figures 8.2.1 and 8.2.2). In this way it is possible to focus the mining on the orebody itself. In some cases, the near-surface part of an orebody is ...
اقرأ المزيدIt is defined as the volume that is occupied by the grinding media out of the total volume of the ball mill without ore or water in it. The ball load should be such that it is slightly more than 30% of the total volume of the ball mill. During general operation media occupy between 30-50% of the volume of the mill.
اقرأ المزيد250 μm [3]. The semiautogenous grinding process is very sus-ceptible to changes in the particle size and mechanical properties of the incoming ore, which can decrease the ore-processing productivity. In response to this prob-lem, up-to-date solutions like the use of an individual disintegration operation for crushed pebbles in a ball
اقرأ المزيدThe partially reduced ore is then smelted in the second unit, and liquid iron is produced. Smelting-reduction technology enables a wide range of coals to be used for iron making. Iron processing - Ores, Smelting, Refining: Iron ores occur in igneous, metamorphic (transformed), or sedimentary rocks in a variety of geologic environments.
اقرأ المزيدProcess. Measurement-control for crushing and screening process is the measurement and control of key equipment and key process parameters to ensure the continuous, stable, and safe operation of ore crushing and screening. In the practice of produc-tion, the crushing and screening process is related to the particle size of raw ore, the particle ...
اقرأ المزيدThe earliest, and simplest method of crushing ore was the use of arrastras. When enough capital was available, stamp mills replaced arrastras at most mines. The following sections take a look at various types of stamp mills, the most common milling facilities at mines of the frontier West. The Trench mill at Silver City, Nevada 1877.
اقرأ المزيدIt mainly includes crushing process control, crushing appliance fault diagnosis, and automatic distributing control. Crushing Process Control. To ensure the …
اقرأ المزيدsizing crusher for clay with 10% of stones. Clay is sticky. sizing crusher is best choice for crushing the sticky material. 1. The crushing work conditions: Raw material: clay with 10% of stones The feeding size: 200 The discharged size: less than 100mm Capacity: 300-400t/h Solutions Model: FP 63AS Power: 200KW Weight: 22 ton Dimension: refer ...
اقرأ المزيدThe multilayer-particle breakage refers to the crushing of multilayer particles held by steel ball-steel ball or steel ball-liner, as shown in Fig. 1(b). In this study, the. Breakage probability. In the milling process, there are many mineral particles in the cylinder with different shapes.
اقرأ المزيدCompared with the original two-stage ball milling process, the cost of grinding power consumption is significantly reduced by about 50.16%, which provides a reference for the subsequent research on energy saving and consumption reduction in ball milling operations. ... [Gao et al., 2020]. Since the ore crushing depend on the …
اقرأ المزيد1,510. Location. West Chester PA. Jul 24, 2019. #4. Ball mill balls wear. They do end up being ground down and are removed at all different sizes. I've worked on ball mills in the upper peninsula (Marquette area) crushing taconite. Pretty sure what you have there is a worn down ball mill ball.
اقرأ المزيدMuch of the remaining iron ore resources in Brazil consist of low-grade itabirite ores. Accordingly, a typical beneficiation circuit includes a four-staged crushing/screening plant, followed by grinding in a closed-circuit ball mill, desliming in hydrocyclones and final ore mineral concentration via multistage reverse flotation and …
اقرأ المزيدRaw mill Raw mill application: Raw ore mill is the key equipment for grinding after the crush process, which is widely used in manufacture industries, such as cement, silicate, new building material, refractory material, fertilizer, ferrous metal, nonferrous metal and glass ceramics and can be used for the dry and wet grinding for all kinds of ores and …
اقرأ المزيدCrushed ore is fed to the ball mill through the inlet; a scoop (small screw conveyor) ensures the feed is constant. For both wet and dry ball mills, the ball mill is charged to approximately 33% with balls (range 30-45%). Pulp (crushed ore and water) fills another 15% of the drum's volume so that the total volume of the drum is 50% charged.
اقرأ المزيدmineral processing, art of treating crude ores and mineral products in order to separate the valuable minerals from the waste rock, or gangue. It is the first process that most ores undergo after mining in order to provide a …
اقرأ المزيدStage 1: Crushing and screening. The large pieces of lead-zinc ore are evenly sent to the jaw crusher or mobile jaw crushing station (primary crushing) by the vibrating feeder through the silo for coarse crushing. The coarsely crushed lead-zinc ore is screened by a vibrating screen, and then sent to a single-cylinder hydraulic cone crusher ...
اقرأ المزيد