TECHNICAL SPECIFICATION OF WET BALL MILL …
The Gravimetric feeder feeds limestone to Wet ball mill system. The Wet Ball Mill system consists of Wet Ball Mill, Wet Ball Mill Lubrication system, Mill circuit …
اقرأ المزيد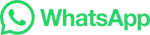
The Gravimetric feeder feeds limestone to Wet ball mill system. The Wet Ball Mill system consists of Wet Ball Mill, Wet Ball Mill Lubrication system, Mill circuit …
اقرأ المزيدContribute to yunan88/crusher development by creating an account on GitHub.
اقرأ المزيدIn response to the Natural Resources Canada "Crush It Challenge," Corem partnered with the University of British Columbia and led a project to develop and demonstrate the use of high-pressure grinding to replace the workhorse of the industry, wet ball milling. Two plant case studies, a small tonnage gold recovery operation and a …
اقرأ المزيد• Edge driving ball mill: the motor drives the gear on the edge of the cylinder through the reducer to drive the cylinder movement. 6. According to the operation characteristics of ball mill: • Wet ball mill: Adding water when feeding, the discharging material is discharged when it is in a certain concentration of slurry. The wet ball mill ...
اقرأ المزيدIn response to the Natural Resources Canada "Crush It Challenge," Corem partnered with the University of British Columbia and led a project to develop and …
اقرأ المزيدHowever, the ball mill has the disadvantages of low working efficiency and high energy-consumption. To improve the grinding performance, the ball mill load must be tweaked to levels where the plant can get desired product size and maximum production rate. However, the ball mill load is difficult to be detected by instruments directly.
اقرأ المزيدThe Planetary Ball Mill PM 100 is a powerful benchtop model with a single grinding station and an easy-to-use counterweight which compensates masses up to 8 kg. It allows for grinding up to 220 ml sample material per …
اقرأ المزيدThere shall be two numbers wet Ball mills for grinding of limestone, each mill shall be sized to meet the following conditions, all occurring together. Capacity 30.2 Tons Per Hour (TPH). Input Limestone Size 1" (max.) – 25 mm. Output Fineness 30 wt. % slurry with Output Fineness 90% or higher through 325 mesh.
اقرأ المزيدWe bring forth a highly advanced Ball Mill, specifically engineered for both wet as well as dry cement grinding applications. Classified depending on the circuit design, bearing, grinding type and drive, the selection is made on …
اقرأ المزيدParticle size reduction of materials in a ball mill with the presence of metallic balls or other media dates back to the late 1800's. The basic construction of a ball mill is a cylindrical container with journals at its axis. The cylinder is filled with grinding media (ceramic or metallic balls or rods), the product to be ground is added and ...
اقرأ المزيدFeurstenau, J.J, Lutch, A. de, (1999) The effect of ball size on the energy efficiency of hybrid pressure roll mill/ ball mill grinding, power technology. 105199-204.
اقرأ المزيدThe Planetary Ball Mill PM 200 is a powerful benchtop model with 2 grinding stations for grinding jars with a nominal volume of 12 ml to 125 ml. The extremely high centrifugal forces of Planetary Ball Mills result in very high pulverization energy and therefore short grinding times. The PM 200 can be found in virtually all industries where the ...
اقرأ المزيدEconomy Ball Mill, a division of JSB Industrial Solutions, Inc. manufactures Ball Mills that are diverse in applications and uses. Since we are an OEM and our product line has been around for over 50 years, we can provide the experience and knowledge to enhance your process capabilities by applying our procedural based manufacturing methods to your …
اقرأ المزيدBall Mill Ball mill machine is widely applied in the industries, such as cement, silicate product, refractory, fertilizer, mineral processing of ferrous and nonferrous metal and glass ceramic, etc It is mainly used to make dry or wet powder grinding of various ores and other grindable materials Working Principle Of Ball Mill:The wet type ball ...
اقرأ المزيدIn general, ball mills can be operated either wet or dry and are capable of producing products on the order of 100 um. This duty represents reduction ratios as great as 100. The ball mill, an intermediate and fine-grinding device, is a tumbling drum with a 40% to 50% filling of balls. ... work screen surfaces in the crushing plant, etc. which ...
اقرأ المزيدThe proven classical option for cement grinding. Whether employed as a two-compartment separator mill in an independent grinding system, or in combination with a high pressure grinding roll, the Ball Mill is a robust and reliable alternative for cement and granulated blast furnace slag grinding.. Used in combination with the sepol® high-efficiency separator, …
اقرأ المزيدThe Rainhart Aggregate Wet Ball Mill is used to determine the resistance of aggregate in flexible base materials to disintegration in the presence of water. These results are essential in determining whether the base will resist crushing, degradation, disintegration, and premature structural failure.
اقرأ المزيدOne modern mill type is a carborundum roller mill (Fig. 10.7). These mills are commonly used in commercial dehulling plants. It has a cylindrical carborundum …
اقرأ المزيدThen in ball-wear formula (25), T = 6.9/K Log10 Da/Db; but from (29), K = Rt/Wt. Then T = 6.9Wt/Rt Log10 Da/Db T is 1 day, Wt is the original weight of the ball charge, and Rt is the ball wear for one day. Then Log10 Da/Db = Rt/6.9Wt are all known, and it is only necessary to solve for Db, the diameter of the balls to be added.
اقرأ المزيدThe cement ball mill is a kind of cement grinding mill.It is mainly used for grinding the clinker and raw materials of the cement plant, and also for grinding various ores in metallurgical, chemical, and electric power …
اقرأ المزيدYet, in Giga factories and large recycling plants, laboratory ball mills still play a primary role in quality control processes when preparing material samples for …
اقرأ المزيدBall mill shells are often furnished with two manholes. Ball mills – with small balls or cylpebs – can produce the finest product of all tumbling mills. 80% minus 74 microns is a normal requirement from the …
اقرأ المزيدThe principle of wet ball milling is based on the energy transfer between the grinding media and the material being ground. In the process of wet ball milling, the grinding media are typically made of steel or ceramics, and they are loaded into the mill in a specific proportion. As the cylinder rotates, the grinding media and the material being ...
اقرأ المزيدSize reduction is a necessary operation in mineral processing plants and provides the desired size for separation operations and the liberation of the valuable minerals present in ores. Estimations on energy consumption indicate that milling consumes more than 50 % of the total energy used in mining operations. Despite the fact …
اقرأ المزيدCall us at 330.929.3333, contact us or click here to find a rep in your area. In discussions on high energy ball milling, the more generic term "ball mills" is often used in place of the terms "stirred ball mills" or "Attritors," but the differences between the types of mills are quite distinct. And, depending on your application, you may find ...
اقرأ المزيدCrushed ore is fed to the ball mill through the inlet; a scoop (small screw conveyor) ensures the feed is constant. For both wet and dry ball mills, the ball mill is charged to approximately 33% with balls (range 30-45%). Pulp (crushed ore and water) fills another 15% of the drum's volume so that the total volume of the drum is 50% charged.
اقرأ المزيدThe ultimate ball mill – with flexibility built in. You can't optimise cement grinding with a one-size-fits-all solution. That's why our ball mills are designed to adapt to your requirements, with a high degree of flexibility built in. You decide whether to operate the mill in open or closed circuit, with or without a pre-grinder and with ...
اقرأ المزيدSand processing by means of a wet ball mill has proven to be an economically advantageous solution for the manufacture of aerated concrete. Masa attach great importance to an efficient plant layout - therefore, we consider important raw material parameters, such as the particle size distribution curve of the sand and the specific size …
اقرأ المزيدCrushed ore is fed to the ball mill through the inlet; a scoop (small screw conveyor) ensures the feed is constant. For both wet and dry ball mills, the ball mill is charged to approximately 33% with balls (range 30-45%). …
اقرأ المزيدHow to choose dry and wet ball mill. 1. Correctly choose the feeding way of dry grinding and wet grinding. Whether feed the material dry or wet depends entirely on …
اقرأ المزيد