Important aspects of Rolling of Hot Rolled Coil in Hot Strip Mill
The range of HSMs for the rolling of hot rolled coils has undergone significant changes in the last few decades with minimum thickness of the hot rolled strips has been decreased from 1.8 mm to 2 mm to 0.8 mm to 1.2 mm. The strips of such thickness were earlier produced only in the cold rolling mills.
اقرأ المزيد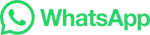