An overview of the beneficiation of iron ores via reverse …
The high potential of flotation for the beneficiation of low-grade oxidised iron ores was emphasised by Iwasaki (1983). According to Peres and Mapa (2008), reverse cationic flotation is critical for producing pellet feed fines at all processing plants in Brazil. 2. Flotation routes for iron ores.
اقرأ المزيد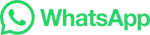