Chemistry KS4/GCSE: How is iron extracted?
Key Stage 3 Help students to make the link between the reactivity of a metal and the methods used to extract it. Because iron is below carbon in the reactivity series, it can be displaced from its ...
اقرأ المزيد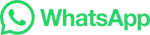