End Mill Sizes [Chart]
Knowing the standard end mill sizes is important for choosing the right tool for creating those parts. Milling bits come in a variety of diameter and styles to meet the demands of any machining design. The standard bit size range is from .005" to 1.25" in diameter for carbide. Most sizes are generally available from stock, and made in the USA.
اقرأ المزيد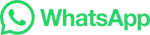