Cement Manufacturing Process
Rotating ball mill. CEMENT MANUFACTURING PROCESS PHASE VI: PACKING AND SHIPPING. Transportation of cement from silos. Material is directly conveyed to the silos (silos are the large storage tanks …
اقرأ المزيد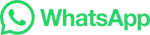
Rotating ball mill. CEMENT MANUFACTURING PROCESS PHASE VI: PACKING AND SHIPPING. Transportation of cement from silos. Material is directly conveyed to the silos (silos are the large storage tanks …
اقرأ المزيدIn this process the limestone and clay are first pre-homogenized, a process that consists of combining different types of limestone and clay. The resulting mix is typically dried, and then prepared for the kiln. ... mixed with gypsum and fed in specified proportions into a cement grinding mill where they are ground into an extremely fine powder ...
اقرأ المزيدConcrete milling is the process of removing the top layers of a concrete surface. It's carried out using scarifying machines equipped with diamond-tipped blades. Milling operations are effective at creating level, smooth surfaces that provide a lot of traction. Plus, the material that's chipped away can be repurposed for aggregate material ...
اقرأ المزيدThe Fig.1. show the flow diagram of the dry process of the manufacture of cement. 1. Dry Process. In the dry and semi-dry process the raw materials are crushed in a dry state. Then, they are processed in grinding mill, dried and reduced to very fine powder-like. That dry power is further blended, corrected for the right composition and …
اقرأ المزيدThis technology has attracted the interest of the cement industry with its proven benefits in cement grinding applications. A process simulator was used to study an industrial-scale vertical raw ...
اقرأ المزيدCement ball mills typically have two grinding chambers. The first chamber is filled with larger diameter grinding media andlined with lifting liners . The first chamber coarse-grinds the feed ... the mill after optimizing the grinding process. rogress of grinding is clearly visible in Desired p the graphs. Figure -2: Analysis of longitudinal ...
اقرأ المزيدCoal Mill In Coal Powder Preparation Process. Coal mill is the main equipment in the pulverized coal preparation process.Because calcining top-grade cement clinker requires a stable supply of coal powder as the fuel of cement kiln, and more than 85% of pulverized coal should be finer than 200 mesh, water content less than 2%, and calorific value more …
اقرأ المزيدDuring heat up there should be a sufficient air flow through the mill to force the heat transfer to the grinding part – forced convection. A sufficient air flow will result in a mill differential pressure of> 5mbar. The duration of heating should be at least until the temperatures after mill and after bag filter reach 85° C.
اقرأ المزيدTherefore, producing cement with less energy is becoming a key element of profitability: as the grinding process consumes about 60 per cent of the total plant electrical energy demand and about 20 per cent of cement production variable cost. So efficient grinding unit selection impacts profitability of cement manufacturing.
اقرأ المزيدIn general, a full cement production process includes the stone crushing, raw mill process, clinker process, and cement grinding process, cement packing process, and related process. The Portland …
اقرأ المزيدA 6-week modular course is designed to give the course attendee a solid understanding of the grinding system and its auxiliary equipment. The purpose of the training is to Identify and understands necessary known and unknown information towards the completed cycle of the grinding system, whether it is a ball mill, vertical mill, or …
اقرأ المزيدAbstract: It is known that the variable is strong coupling, nonlinear, multivariable and large time-delay dynamic characteristics in the raw cement vertical mill grinding process. …
اقرأ المزيدGrinding occurs at the beginning and the end of the cement making process. Approximately 1.5 tonnes of raw materials are required to produce 1 tonne of …
اقرأ المزيدCement ball mills typically have two grinding chambers. The first chamber is filled with larger diameter grinding media andlined with lifting liners . The first chamber coarse-grinds the feed ... the mill after optimizing the grinding process. rogress of grinding is clearly …
اقرأ المزيدThe grinding process can be done in ball or tube mill or even both. Then the slurry is led into collecting basin where composition can be adjusted. The slurry contains around 38-40% water that is stored in storage tanks and kept ready for the rotary kiln. Fig: Manufacture of Cement by Wet Process
اقرأ المزيدThe cement mill can be used as a raw mill or cement grinding mill, AGICO Cement provides vertical cement mill, cement ball mill and other high-quality cement grinding machines for you! ... For a complete project: the material availability, the required output capacity, the process technology, your budgetary and financing status, the estimated ...
اقرأ المزيدMaterial is directly conveyed to the silos (silos are the large storage tanks of cement) from the grinding mills. Further, it is packed to about 20-40 kg bags. ... After explaining the complete process of cement making, flow chart would be like that. flow chart present the summary of whole process as shown below.
اقرأ المزيدCement grinding operation may be performed in one of the following mill setups. Ball and tube mills. Vertical Roller Mills (VRM). Roller press with Ball mill. Ball Mill. Ball mills …
اقرأ المزيدThe final manufacturing stage at a cement plant is the grinding of cement clinker from the kiln, mixed with 4-5% gypsum and possible additives, into the final product, cement . In a modern cement plant the total consumption of electrical energy is about 100 kWh/t . The cement grinding process accounts for approx. 40% if this energy consumption.
اقرأ المزيدHere is a step-by-step procedure for the wet process of Cement manufacture: Quarrying and Crushing: The raw materials, such as Limestone, clay, and iron ore, are extracted from quarries and then …
اقرأ المزيدIn this study, a nonlinear dynamic model of a cement grinding process, including a ball mill and an air separator in closed loop, is developed. This gray-box …
اقرأ المزيدAs the name implies, in the batch mills, Fig. 1.4a, the charge of powder to be ground is loaded into the mill in a batch and, after the grinding process is completed, is removed in a batch. Clearly such a mode of operation can only be applied to mills of small or moderate sizes; say to mills of up to about 7 ft diameter by about 7 ft long.
اقرأ المزيدThe ultimate ball mill – with flexibility built in. You can't optimise cement grinding with a one-size-fits-all solution. That's why our ball mills are designed to adapt to your requirements, with a high degree of flexibility built in. You decide whether to operate the mill in open or closed circuit, with or without a pre-grinder and with ...
اقرأ المزيدGenerally, the proportion of components in cement raw materials is 67-75% limestone, 10-15% clay, 0.5-1.5% iron ore and 8.5-11% coal. The laboratory of a cement plant. With the help of vertical roller mills or other types of crushers, the raw materials are blended and further ground into smaller pieces of raw meal in the cement plant.
اقرأ المزيدThe optimization of this process would yield substantial benefits in terms of energy savings and capacity increase. 1. Optimization of the Cement Ball Mill Operation. Optimization addresses the grinding process, maintenance and product quality. The objective is to achieve a more efficient operation and increase the production rate as well as ...
اقرأ المزيدAbstract: It is known that the variable is strong coupling, nonlinear, multivariable and large time-delay dynamic characteristics in the raw cement vertical mill grinding process. Against the problem which is difficult to establish accurate mathematical model, this paper establishes a production index prediction model of vertical mill raw meal grinding …
اقرأ المزيدFrom the crushing and grinding of raw materials to the final production of cement, our grinding mill products play a crucial role throughout the entire process. To …
اقرأ المزيدAbstract. Grinding is an essential operation in cement production given that it permits to obtain fine powder which reacts quickly with water, sets in few hours and hardens over a period of weeks ...
اقرأ المزيدcement ball mill. Application: limestone, clay, coal, feldspar, calcite, talc, iron ore, copper, phosphate, graphite, quartz, slag. Capacity: 0.65-615T/H. The cement ball mill usually can be applied to raw meal grinding or cement grinding. Besides, the cement ball mill also can be used for metallurgical, chemical, electric power, other mining ...
اقرأ المزيدThe energy consumption of the total grinding plant can be reduced by 20–30 % for cement clinker and 30–40 % for other raw materials. The overall grinding circuit …
اقرأ المزيد