(PDF) Iron Ore Pelletizing Process: An Overview
The iron ore pelletizing process consists of three main steps: 1. Pelletizing feed preparation and mixing: the raw material (iron ore concentrate, additives. — anthracite, dolomite — and ...
اقرأ المزيد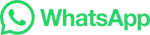