Coal utilisation in the cement and concrete industries
The utilisation of coal in the cement and concrete industries takes three basic forms: 1. As a fuel in the production of cement clinker, 2. Ash produced by burning …
اقرأ المزيد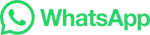
The utilisation of coal in the cement and concrete industries takes three basic forms: 1. As a fuel in the production of cement clinker, 2. Ash produced by burning …
اقرأ المزيدThe manufacture procedures of Portland cement is described below. Mixing of raw material. Burning. Grinding. Storage and packaging. 1. Mixing of raw material. The major raw materials used in the manufacture of cement are …
اقرأ المزيدWhat role does coal play in cement production? Coal plays a very important role for manufacturing plants is undeniable. In many applications from gasification technology, liquefaction, production of …
اقرأ المزيدPortland cement is by far the most common type of cement in general use around the world. This articles looks at the cement manufacturing process in 4 steps. Step 1: Mining. The first step of …
اقرأ المزيدcement industry Measuring point 1 (Process) 2 (Process) 3 (Safety) 4.1 (Safety) 4.2 (Safety) 5.1 (Emission) 5.2 (Emission) Application Measuring task Measuring components Analyzers Analyzer system Kiln gas outlet Calciner Preheater Coal bin Coal mill Emission Emission – Optimization of primary firing – Lower fuel consumption
اقرأ المزيدThere are four stages in the manufacture of portland cement: (1) crushing and grinding the raw materials, (2) blending the materials in the correct proportions, (3) burning the prepared mix in a kiln, and (4) grinding the burned product, known as " clinker," together with some 5 percent of gypsum (to control the time of set of the cement).
اقرأ المزيدStage of Cement Manufacture. There are six main stages of the cement manufacturing process. Stage 1: Raw Material Extraction/Quarry The raw cement ingredients needed for cement production are limestone (calcium), sand and clay (silicon, aluminum, iron), shale, fly ash, mill scale, and bauxite. The ore rocks are quarried and crushed into smaller …
اقرأ المزيدHere are the five stages of the cement production process and the steps to maintain consistent cement raw material quality with minimal chemistry deviation, ... Coal Mill Coal is still used in approximately 90% of cement plants globally to deliver the energy needed for the heat inside the kiln. Online coal analyzers using PGNAA technology are ...
اقرأ المزيدThe coal mill uses coal, coke or grinded pet coke with different size of balls. Larger sized balls are used for impact grinding and the smaller balls are used for attrition grinding. 3.1.8. Cement mill. This is the final step in a cement manufacturing process. In this step, the clinker is ground together with additives in a cement mill.
اقرأ المزيدThe primary cement manufacturing process involves the mining of raw materials, mainly limestone and clay, which are used in cement manufacturing. In most of the cases, the limestone and clay are excavated from open cast mines by drilling and blasting and other appropriate processes in mines. Subsequently, the limestone and …
اقرأ المزيدThe cement production process. The cement production process begins with the extraction of limestone and clay from the quarry. The material is then blended, crushed and fed to the kiln. Post-kiln, the clinker is cooled and goes through a final grinding method before it is ready to ship. Portland cement, the most common type of cement, is ...
اقرأ المزيدIt is a mechanical device used to grind raw coal into pulverized coal powders. The most used coal mills in cement plants are air-swept ball mills and vertical roller mills. At present, most cement plants use coal as the main fuel in the clinker production process. The standard coal consumed by the new dry process for producing 1 ton of cement ...
اقرأ المزيد1. Introduction. Nowadays, cement manufacturing is an energy-intensive industry. The energy costs of cement industry are about 40% of the product cost that indicates that this sector is one of the biggest CO 2 emitter. The global anthropogenic CO 2 emission of cement industry is approximately 5% [].The International Energy Agency …
اقرأ المزيدAbout Us Purchasing Process Alternative Solid Fuels Evaluation Recommendations Partners Specification System Layout Assistance. Coal Mill Safety In Cement Production Industries. It may come as a surprise, but cement industry is not capturing nearly as many coal dust explosions that actually occur. These incidents are often reported as boiler ...
اقرأ المزيدThe cement production process 1. The Quarry: The cement production process begins with the extraction of limestone and clay from the quarry. 2. Crusher and Pre-Blending: The material is then crushed to reduce particle sizes and blended to reduce variability in composition. 3. Raw Mill and Kiln: Raw materials and additives are
اقرأ المزيدThe results show that approximately 2.48t, 4.69t, and 3.41t of materials are required to produce a ton of the product in raw material preparation, clinker production, and cement grinding stages ...
اقرأ المزيدThe typical cement manufacturing process involves the following steps: limestone quarrying, raw material preparations by crushing and milling, preheating, pre-calcining, kiln firing, ... 0.025 kg from the clinker cooler and 0.010 kg from the coal mill, per ton of clinker. Total 0.081 kg of particulate matter/ton of clinker was emitted during ...
اقرأ المزيدCement C3S, C2S, C3A, C4AF. Burnability index (for clinker) Burnability factor (for clinker) Burning temperature (minimum) Go To Online Calculators. 28-days mortar strength Mpa. Gypsum Set Point (GSP) Go To Online Calculators. False air calculations, heat loss calculations, LSF, Silica modulus, alumina modulus, calorific value, minimum ...
اقرأ المزيدget price! Air-swept coal mill is the main equipment of cement plant, also called coal mill in cement plant, used for grinding and drying various hardness of coal, crushing the …
اقرأ المزيدGenerally, the proportion of components in cement raw materials is 67-75% limestone, 10-15% clay, 0.5-1.5% iron ore and 8.5-11% coal. The laboratory of a cement plant. With the help of vertical roller mills or other types of crushers, the raw materials are blended and further ground into smaller pieces of raw meal in the cement plant.
اقرأ المزيدExternal Thermal Efficiency is using the recovered heat for other process; Raw mill, Coal Mill and Cement mill drying; Heating and power generation; Speed of Clinker Cooling. Rapid cooling. prevents growth of crystals and its size; gives suitable clinker nodule; solidify the clinker in to glass state; Improve C 3 S and reduce C 2 S leads to ...
اقرأ المزيدThe quadropol® concept for coal or pet coke grinding, with adapted table speed and high efficiency separator sepol®, ensures a safety mill operation and serves reliable the kiln burning process. Mombasa Cement Ltd. ordered a QMK² 24/12 with three roller units for the 5,000 tons per day kiln line.
اقرأ المزيدThe cement industry has reduced CO 2 emissions per tonne by 50% between 1990 and 2020 by increasing the use of non-fossil fuels. The Mineral Production Association Cement 4 (MPA Cement) proposes two scenarios for further carbon reduction.. . Proposal 1: by 2050 to reduce carbon release per tonne of cement by 62% compared to the value in …
اقرأ المزيدThe cement manufacturing process starts from the mining of raw materials like limestone, clay used mainly in the manufacturing process. A limestone mines are opencast type and is nearby plant area and clays mines also found nearby to save transportation cost. ... Coal is ground in Coal mill, which is a fuel for use in Kiln firing: 5: …
اقرأ المزيدIn terms of coal utilization in the cement-manufacturing process, its use as a fuel in rotary kilns is the main area of consideration. 18.3.6. ... Most coal mill designs are based upon a 50–55 HGI design point. However, grindability is a complex issue and factors such as coal moisture content and required fineness ...
اقرأ المزيدThe use of fossil fuels such as coal, natural gas, and oil is common in cement production, both as a fuel for the kiln and as a source of heat for other parts of the process which leads to CO2 emitted by combustion.However chemical reactions happening in the kiln (calcination) are also responsible for up to 60% of the total of emissions of the ...
اقرأ المزيدCement manufacturing is a complex process that begins with mining, drying, and then grinding raw materials. The main raw material is calcium carbonate (CaCO 3) from …
اقرأ المزيدOther types of roller mills such as ball race mill (Fuller-Peters mill) and Raymond bowl-type ring mill are used in coal grinding. 2.4. CKP vertical pre-grinder ... Vol. 1, International Process Engineering in the Cement Industry. French & European Pubns. 3rd edition; 1985. 9. Nobis R. Experience with grinding slag and clinker in a Loesche mill.
اقرأ المزيدPyroprocessing is the most energy intensive process in overall cement production. It consumes about 91% of the total energy used in the cement manufacturing process (Treloar 1998). Pyroprocessing consists of three stages, including pre-heating, heating of raw materials in rotary kiln by burning of fuels and cooling the clinker collected …
اقرأ المزيد1 Potential safety hazards in the coal mill system. 1.1 Spontaneous combustion occurs. The process of cement production determines the need to use a large amount of coal. The use of coal is mostly ...
اقرأ المزيد