[PDF] Detailed Modeling of the Direct Reduction of Iron Ore …
This paper addresses the modeling of the iron ore direct reduction process, a process likely to reduce CO2 emissions from the steel industry, using a multi-scale approach and finds the presence of a central zone of lesser temperature and conversion. This paper addresses the modeling of the iron ore direct reduction process, a process likely to …
اقرأ المزيد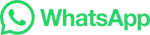