Lithium processing technology Complete solutions that …
Spodumene ores are typically consolidated from ore comprising 1–1.5% Li20 to a concentrate of about 6–6.5% Li20. To achieve this, the ore passes through a typical concentrator-type plant, flowing from crushing and grinding, to gravity separation and DMS, to flotation, and then to the final dewatering of the concentrate.
اقرأ المزيد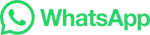